Vertical Shell&tube type of heat exchanger
1. Definition and Purpose:
Clearly define what a vertical heat exchanger is, emphasizing the vertical orientation of heat transfer surfaces.
Explain its purpose, which often involves leveraging gravity for fluid flow, like in condensers, or utilizing space-saving design.
2. Types and Configurations:
Vertical Shell and Tube Heat Exchangers:
These have tubes arranged vertically within a cylindrical shell.
Vertical Plate Heat Exchangers:
These use thin, corrugated plates arranged vertically, offering compact designs.
Vertical Tubular Heat Exchangers:
These can be either single or multiple tubes, with vertical orientation for specific applications.
Vertical Spiral Heat Exchangers:
These have a spiral configuration with vertical flow paths, offering high heat transfer rates and space efficiency.
3. Advantages:
Gravity-Assisted Flow:
Vertical orientation can facilitate natural circulation in some applications, simplifying pumping requirements.
Space Savings:
Vertical configurations can be more compact than horizontal designs, especially for high heat transfer requirements.
Enhanced Mixing:
The vertical orientation can promote better mixing of fluids within the shell, improving heat transfer efficiency.
4. Disadvantages:
Limited Tube Length:
Vertical designs may have limitations in tube length due to structural considerations and potential issues with flow dynamics.
Maintenance:
Vertical shell and tube heat exchangers can be more challenging to clean and maintain than horizontal designs.
High Pressure Drop:
Vertical designs may experience higher pressure drops compared to horizontal designs due to the effects of gravity on fluid flow.
5. Applications:
Condensers:
Vertical heat exchangers are used for condensing steam or vapor, with gravity aiding condensation.
Cooling Tower Design:
Vertical designs can be used in cooling towers to facilitate heat dissipation through water evaporation.
Boiler and Heat Recovery Systems:
Vertical heat exchangers are used to recover heat from flue gases or other industrial processes.
Space-Constrained Applications:
Vertical designs are suitable for areas where vertical space is available but horizontal space is limited.
Here's a more detailed description:
Purpose:
1.Shell & tube type heat exchanger
2.U tube type heat exchanger
3.fixed tube-to-tubesheet heat exchanger
4.floting head bundle
5. heat exchanger maintenance
Leak Detection:
Pneumatic tests help identify leaks in heat exchangers by observing for pressure loss or by using a soap solution to detect leaks at joints and connections.
Integrity Verification:
The test ensures the exchanger can withstand the design pressure and that all welds and joints are sound.
Procedure
1. Preparation:
The heat exchanger is cleaned, dried, and prepared for testing.
2. Pressurization:
The heat exchanger is filled with air or nitrogen to a specified pressure, usually 1.1 times the maximum allowable working pressure (MAWP).
3. Leak Detection:
Pressure is monitored for any loss, and joints are checked for leaks using a soap solution.
4. Duration:
The test pressure is maintained for a minimum time, typically 10-15 minutes.
5. Evaluation:
The exchanger is assessed for any leaks, and the test is considered passed if no leaks are detected.
Safety Considerations:
Compressed Gas Hazards:
Due to the potential for explosive release of compressed gas in case of a failure, safety precautions are essential.
Pressure Relief Devices:
Pressure relief valves or other devices should be installed to prevent overpressure.
Personnel Protection:
Personnel should be kept at a safe distance during the test and be shielded from potential projectiles in case of failure.
When to Use:
Water Not Suitable:
When water cannot be used as the test medium, such as in certain tube-to-tubesheet joints.
Specific Applications:
For applications where rapid pressurization and shorter test durations are needed, or for testing gas systems.
Видео Vertical Shell&tube type of heat exchanger канала Oil&Gas world
Clearly define what a vertical heat exchanger is, emphasizing the vertical orientation of heat transfer surfaces.
Explain its purpose, which often involves leveraging gravity for fluid flow, like in condensers, or utilizing space-saving design.
2. Types and Configurations:
Vertical Shell and Tube Heat Exchangers:
These have tubes arranged vertically within a cylindrical shell.
Vertical Plate Heat Exchangers:
These use thin, corrugated plates arranged vertically, offering compact designs.
Vertical Tubular Heat Exchangers:
These can be either single or multiple tubes, with vertical orientation for specific applications.
Vertical Spiral Heat Exchangers:
These have a spiral configuration with vertical flow paths, offering high heat transfer rates and space efficiency.
3. Advantages:
Gravity-Assisted Flow:
Vertical orientation can facilitate natural circulation in some applications, simplifying pumping requirements.
Space Savings:
Vertical configurations can be more compact than horizontal designs, especially for high heat transfer requirements.
Enhanced Mixing:
The vertical orientation can promote better mixing of fluids within the shell, improving heat transfer efficiency.
4. Disadvantages:
Limited Tube Length:
Vertical designs may have limitations in tube length due to structural considerations and potential issues with flow dynamics.
Maintenance:
Vertical shell and tube heat exchangers can be more challenging to clean and maintain than horizontal designs.
High Pressure Drop:
Vertical designs may experience higher pressure drops compared to horizontal designs due to the effects of gravity on fluid flow.
5. Applications:
Condensers:
Vertical heat exchangers are used for condensing steam or vapor, with gravity aiding condensation.
Cooling Tower Design:
Vertical designs can be used in cooling towers to facilitate heat dissipation through water evaporation.
Boiler and Heat Recovery Systems:
Vertical heat exchangers are used to recover heat from flue gases or other industrial processes.
Space-Constrained Applications:
Vertical designs are suitable for areas where vertical space is available but horizontal space is limited.
Here's a more detailed description:
Purpose:
1.Shell & tube type heat exchanger
2.U tube type heat exchanger
3.fixed tube-to-tubesheet heat exchanger
4.floting head bundle
5. heat exchanger maintenance
Leak Detection:
Pneumatic tests help identify leaks in heat exchangers by observing for pressure loss or by using a soap solution to detect leaks at joints and connections.
Integrity Verification:
The test ensures the exchanger can withstand the design pressure and that all welds and joints are sound.
Procedure
1. Preparation:
The heat exchanger is cleaned, dried, and prepared for testing.
2. Pressurization:
The heat exchanger is filled with air or nitrogen to a specified pressure, usually 1.1 times the maximum allowable working pressure (MAWP).
3. Leak Detection:
Pressure is monitored for any loss, and joints are checked for leaks using a soap solution.
4. Duration:
The test pressure is maintained for a minimum time, typically 10-15 minutes.
5. Evaluation:
The exchanger is assessed for any leaks, and the test is considered passed if no leaks are detected.
Safety Considerations:
Compressed Gas Hazards:
Due to the potential for explosive release of compressed gas in case of a failure, safety precautions are essential.
Pressure Relief Devices:
Pressure relief valves or other devices should be installed to prevent overpressure.
Personnel Protection:
Personnel should be kept at a safe distance during the test and be shielded from potential projectiles in case of failure.
When to Use:
Water Not Suitable:
When water cannot be used as the test medium, such as in certain tube-to-tubesheet joints.
Specific Applications:
For applications where rapid pressurization and shorter test durations are needed, or for testing gas systems.
Видео Vertical Shell&tube type of heat exchanger канала Oil&Gas world
Комментарии отсутствуют
Информация о видео
2 мая 2025 г. 22:30:02
00:01:00
Другие видео канала
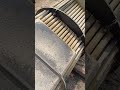

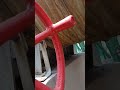

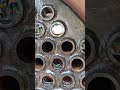
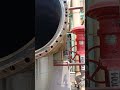
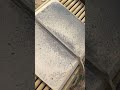

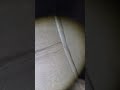

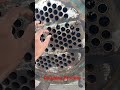
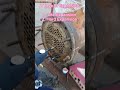
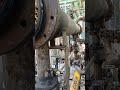


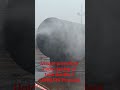
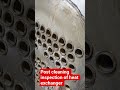


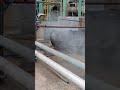