Spare Parts #11 - Making A 4 Flute Light Duty Dovetail Cutter
Making A 4 Flute Light Duty Dovetail Cutter, by Clickspring.
The "Impossible Dovetail" project requires a rather unique narrow taper dovetail cutter. So in this video I make my own from oil hardening (O1) tool steel. There's plenty of lathe and mill work in the project, as well as hardening and tempering of the cutting tool with basic shop equipment.
The "Impossible Dovetail" project can be found here: https://youtu.be/a3V42KwLTeE
If you would like to help support the creation of these videos, then head on over to the Clickspring Patreon page: https://www.patreon.com/clickspring
You can also help me make these videos by purchasing via the following Amazon Affiliate links:
Cameras used in this video:
Panasonic GH5 - https://amzn.to/2rEzhh2
Panasonic X920 - https://amzn.to/2wzxxdT
Tools & Shop Products:
"Lathework: A Complete Course (Workshop Practice Series)" - https://amzn.to/2yBv4Rb
"Basic Lathework (Workshop Practice Series)" - https://amzn.to/2twVNIU
"Milling: A Complete Course (Workshop Practice Series)" - https://amzn.to/2K2QZ97
"Hardening, Tempering and Heat Treatment (Workshop Practice Series)" - https://amzn.to/2KbZo6l
Dykem 80300 Steel Blue Layout Fluid, Brush-in-Cap (4oz): http://amzn.to/2HGPaJJ
Blue Matador Abrasive Paper - https://amzn.to/2IAFiBT
Kaowool 24" X 12" X 1" 2400 F Ceramic Fiber Insulation: http://amzn.to/2pfsM3d
Saint Gobain (Norton) - 4 Arkansas Stones + case: http://amzn.to/2HCOAMX
Abbreviated Transcript:
00:06 One of the cutting tools required to make this impossible dovetail puzzle is a narrow taper dovetail cutter like this. It has an included angle of 22 degrees, and 4 teeth formed by milling 4 straight flutes.
00:19 Each tooth has positive rake generated from the way the flutes are milled past the centerline, and I'll grind in some relief angles behind each tooth after its been hardened.
00:30 The first step was to turn the basic profile to shape.
01:10 The cutting teeth need to be concentric with this shank, so I'm removing the 3 jaw chuck, and using an ER Collet chuck from here on, to give a better result.
01:33 There's quite a bit of work sticking out from the collet, and its all supported by that narrow shank, so a bit of tailstock support will be needed to get an accurate cut. Once that support was in place, I formed the tapered profile of the cutter.
02:30 At this point the workpiece is essentially a cutter blank, ready to have some teeth formed, so the next step was to transfer it to the mill to cut the 4 flutes.
03:13 Now that most of the shaping of the cutter is complete, it can be taken to a red heat, quenched in oil to harden, and then slowly tempered it to a light straw color.
03:30 Now ideally I'd form the relief angles using a tool cutter grinder, but I don't have one, so I'm freehand grinding them using this bench grinder. I'm keeping the contact with the wheel quite short to keep the heat generated to a minimum, I don't want the temperature to rise so much that it softens those cutting edges.
03:54 And at this point the cutter is basically complete, it just needs to have the small burrs removed, and the cutting edges honed. And I found that its a particularly easy cutter sharpen; it sits comfortable on the bench, and a small oilstone runs neatly down the flutes.
04:14 OK, so with all edges honed and ready to cut, give it a run and see how it performs. I've used a standard end mill to remove the bulk of the waste stock from this test piece of aluminium, so that I put the lowest possible burden on the cutter. And for the most part, it seems to perform quite well. As always though, there are some limitations.
04:32 For one thing it can't be run very hard. If the cutter heats up too much, the carbon steel will become annealed, and immediately lose its cutting edge. Its a light duty cutter suited to relatively soft materials.
04:44 The speed of the cut at the top of the tool is also much slower than at the bottom, and the cutting geometry at the top is less than perfect too. So while the bottom is forming nice chips, the top is a little more inclined to rub the metal rather than cut it.
05:00 It wasn't a huge issue, and a partial solution was to take a finishing pass on either side, as well as use some abrasive paper to knock down the burr, but still, it's not ideal.
05:08 And finally, it's unlikely that the taper I formed on the lathe has survived my freehand grinding of the relief angles, particularly as I resharpen it.
05:16 The accuracy was fine for the project I used this cutter on, but I think its fair to say that freehand grinding of the relief limits the cutter to relatively low precision work like profiling and contouring.
05:28 Having said all that, it cuts aluminium surprisingly well, and seems like a reasonable option for low volume, low precision work in softer materials, particularly if there's nothing available commercially.
Making A 4 Flute Light Duty Dovetail Cutter, by Clickspring.
Видео Spare Parts #11 - Making A 4 Flute Light Duty Dovetail Cutter канала Clickspring
The "Impossible Dovetail" project requires a rather unique narrow taper dovetail cutter. So in this video I make my own from oil hardening (O1) tool steel. There's plenty of lathe and mill work in the project, as well as hardening and tempering of the cutting tool with basic shop equipment.
The "Impossible Dovetail" project can be found here: https://youtu.be/a3V42KwLTeE
If you would like to help support the creation of these videos, then head on over to the Clickspring Patreon page: https://www.patreon.com/clickspring
You can also help me make these videos by purchasing via the following Amazon Affiliate links:
Cameras used in this video:
Panasonic GH5 - https://amzn.to/2rEzhh2
Panasonic X920 - https://amzn.to/2wzxxdT
Tools & Shop Products:
"Lathework: A Complete Course (Workshop Practice Series)" - https://amzn.to/2yBv4Rb
"Basic Lathework (Workshop Practice Series)" - https://amzn.to/2twVNIU
"Milling: A Complete Course (Workshop Practice Series)" - https://amzn.to/2K2QZ97
"Hardening, Tempering and Heat Treatment (Workshop Practice Series)" - https://amzn.to/2KbZo6l
Dykem 80300 Steel Blue Layout Fluid, Brush-in-Cap (4oz): http://amzn.to/2HGPaJJ
Blue Matador Abrasive Paper - https://amzn.to/2IAFiBT
Kaowool 24" X 12" X 1" 2400 F Ceramic Fiber Insulation: http://amzn.to/2pfsM3d
Saint Gobain (Norton) - 4 Arkansas Stones + case: http://amzn.to/2HCOAMX
Abbreviated Transcript:
00:06 One of the cutting tools required to make this impossible dovetail puzzle is a narrow taper dovetail cutter like this. It has an included angle of 22 degrees, and 4 teeth formed by milling 4 straight flutes.
00:19 Each tooth has positive rake generated from the way the flutes are milled past the centerline, and I'll grind in some relief angles behind each tooth after its been hardened.
00:30 The first step was to turn the basic profile to shape.
01:10 The cutting teeth need to be concentric with this shank, so I'm removing the 3 jaw chuck, and using an ER Collet chuck from here on, to give a better result.
01:33 There's quite a bit of work sticking out from the collet, and its all supported by that narrow shank, so a bit of tailstock support will be needed to get an accurate cut. Once that support was in place, I formed the tapered profile of the cutter.
02:30 At this point the workpiece is essentially a cutter blank, ready to have some teeth formed, so the next step was to transfer it to the mill to cut the 4 flutes.
03:13 Now that most of the shaping of the cutter is complete, it can be taken to a red heat, quenched in oil to harden, and then slowly tempered it to a light straw color.
03:30 Now ideally I'd form the relief angles using a tool cutter grinder, but I don't have one, so I'm freehand grinding them using this bench grinder. I'm keeping the contact with the wheel quite short to keep the heat generated to a minimum, I don't want the temperature to rise so much that it softens those cutting edges.
03:54 And at this point the cutter is basically complete, it just needs to have the small burrs removed, and the cutting edges honed. And I found that its a particularly easy cutter sharpen; it sits comfortable on the bench, and a small oilstone runs neatly down the flutes.
04:14 OK, so with all edges honed and ready to cut, give it a run and see how it performs. I've used a standard end mill to remove the bulk of the waste stock from this test piece of aluminium, so that I put the lowest possible burden on the cutter. And for the most part, it seems to perform quite well. As always though, there are some limitations.
04:32 For one thing it can't be run very hard. If the cutter heats up too much, the carbon steel will become annealed, and immediately lose its cutting edge. Its a light duty cutter suited to relatively soft materials.
04:44 The speed of the cut at the top of the tool is also much slower than at the bottom, and the cutting geometry at the top is less than perfect too. So while the bottom is forming nice chips, the top is a little more inclined to rub the metal rather than cut it.
05:00 It wasn't a huge issue, and a partial solution was to take a finishing pass on either side, as well as use some abrasive paper to knock down the burr, but still, it's not ideal.
05:08 And finally, it's unlikely that the taper I formed on the lathe has survived my freehand grinding of the relief angles, particularly as I resharpen it.
05:16 The accuracy was fine for the project I used this cutter on, but I think its fair to say that freehand grinding of the relief limits the cutter to relatively low precision work like profiling and contouring.
05:28 Having said all that, it cuts aluminium surprisingly well, and seems like a reasonable option for low volume, low precision work in softer materials, particularly if there's nothing available commercially.
Making A 4 Flute Light Duty Dovetail Cutter, by Clickspring.
Видео Spare Parts #11 - Making A 4 Flute Light Duty Dovetail Cutter канала Clickspring
Показать
Комментарии отсутствуют
Информация о видео
Другие видео канала
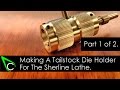
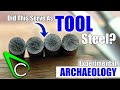
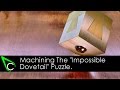

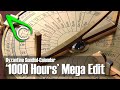
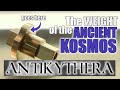

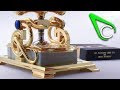
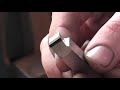

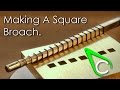
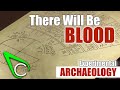
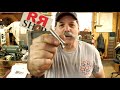
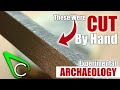
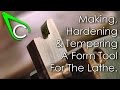
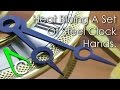
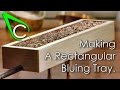
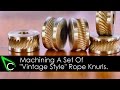

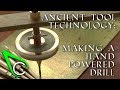