Restoration and Replication of Steel Elements at Fallingwater and Guggenheim Museum
Frank Lloyd Wright used steel windows and doors in innovative ways for his time. At Fallingwater, a weekend home designed for the Kaufmann family of Pittsburgh, he incorporated Hope’s steel casement and fixed windows to create a dramatic effect, often without corner mullions or dying directly into the stone walls with no frame. For the Solomon R. Guggenheim Museum, he employed Hope’s window-walls on the Thannhauser Pavilion.
WASA/Studio A served as preservation architect for both structures. In the case of Fallingwater (1936-39), cantilevered over a stream, the steel elements were found to be significantly corroded and had to be stripped to bare metal. Fixed windows in the main house had no drip edge at the head; this was corrected subsequently for the guest-house addition. Both the heads and sills lack waterproofing, and deformation of the concrete roofs and terraces left enlarged gaps that promoted moisture penetration. This was further exacerbated by the curved profile of roof edges, which also do not include a drip. In several units, areas of deteriorated steel had to be cut out and new sections welded on. The hatch over the stairs to the stream, an iconic element within the living room, was so severely corroded it had not worked in years. A specialty steel-window contractor, Seekircher Steel Window Repair of Scarsdale, NY, executed the work. In addition, when the stairs to the stream were reconstructed, the mild-steel straps from which they were hung had caused the ongoing deterioration of the cast-in-place concrete treads; these were replaced with stainless steel. WASA/Studio A specified the industrial-paint system for all exterior steel elements, which in the case of the stairs to the stream, had to also withstand partial submersion.
By contrast, at the Solomon R. Guggenheim Museum (1959), the original steel window-walls were in excellent condition. However, the high relative humidity in the museum’s interior environment, favorable to the artwork on display, resulted in extreme condensation at the single-glazed window-walls, rendering the Thannhauser Pavilion unusable during the winter months. In this case, with the assistance of William B. Rose Associates, our building-envelope sub-consultant, we undertook a thorough investigation into the efficacy of retrofitting the existing frames, including evaluation of the aesthetic impact (the building is also a NYC-designated interior), as well performance. It was concluded that the window-walls could not be reliably upgraded, nor could the introduction of storm windows guarantee the resolution of the condensation issues. Therefore, we specified steel-framed replicas that were thermally-broken and double-glazed, unprecedented in the US at the time, which were custom-fabricated by Torrance Steel Window Co. out of Torrance, CA.
Although in both cases, Frank Lloyd Wright relied on single-glazed steel-frame windows and doors, our philosophical approach to Fallingwater was completely different from that of the Solomon R. Guggenheim Museum. Fallingwater is a house museum, and the house is interpreted and presented in the way the Kaufmanns lived in it. As such, the windows and doors are open during the months of good weather. Despite the fact that there is important artwork from the Kaufmann’s personal collection displayed in the main house and guest house, these are intentionally not kept in a museum environment. This condition is reversed at the Solomon R. Guggenheim Museum, where authenticity of use – that of a world-class museum – had to take precedence over authenticity of fabric.
Видео Restoration and Replication of Steel Elements at Fallingwater and Guggenheim Museum канала ncptt
WASA/Studio A served as preservation architect for both structures. In the case of Fallingwater (1936-39), cantilevered over a stream, the steel elements were found to be significantly corroded and had to be stripped to bare metal. Fixed windows in the main house had no drip edge at the head; this was corrected subsequently for the guest-house addition. Both the heads and sills lack waterproofing, and deformation of the concrete roofs and terraces left enlarged gaps that promoted moisture penetration. This was further exacerbated by the curved profile of roof edges, which also do not include a drip. In several units, areas of deteriorated steel had to be cut out and new sections welded on. The hatch over the stairs to the stream, an iconic element within the living room, was so severely corroded it had not worked in years. A specialty steel-window contractor, Seekircher Steel Window Repair of Scarsdale, NY, executed the work. In addition, when the stairs to the stream were reconstructed, the mild-steel straps from which they were hung had caused the ongoing deterioration of the cast-in-place concrete treads; these were replaced with stainless steel. WASA/Studio A specified the industrial-paint system for all exterior steel elements, which in the case of the stairs to the stream, had to also withstand partial submersion.
By contrast, at the Solomon R. Guggenheim Museum (1959), the original steel window-walls were in excellent condition. However, the high relative humidity in the museum’s interior environment, favorable to the artwork on display, resulted in extreme condensation at the single-glazed window-walls, rendering the Thannhauser Pavilion unusable during the winter months. In this case, with the assistance of William B. Rose Associates, our building-envelope sub-consultant, we undertook a thorough investigation into the efficacy of retrofitting the existing frames, including evaluation of the aesthetic impact (the building is also a NYC-designated interior), as well performance. It was concluded that the window-walls could not be reliably upgraded, nor could the introduction of storm windows guarantee the resolution of the condensation issues. Therefore, we specified steel-framed replicas that were thermally-broken and double-glazed, unprecedented in the US at the time, which were custom-fabricated by Torrance Steel Window Co. out of Torrance, CA.
Although in both cases, Frank Lloyd Wright relied on single-glazed steel-frame windows and doors, our philosophical approach to Fallingwater was completely different from that of the Solomon R. Guggenheim Museum. Fallingwater is a house museum, and the house is interpreted and presented in the way the Kaufmanns lived in it. As such, the windows and doors are open during the months of good weather. Despite the fact that there is important artwork from the Kaufmann’s personal collection displayed in the main house and guest house, these are intentionally not kept in a museum environment. This condition is reversed at the Solomon R. Guggenheim Museum, where authenticity of use – that of a world-class museum – had to take precedence over authenticity of fabric.
Видео Restoration and Replication of Steel Elements at Fallingwater and Guggenheim Museum канала ncptt
Показать
Комментарии отсутствуют
Информация о видео
Другие видео канала
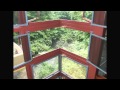
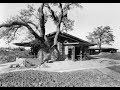
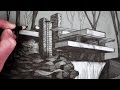
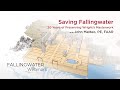

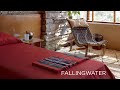
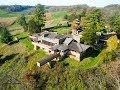
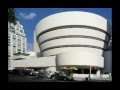

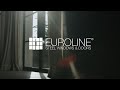
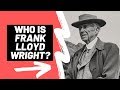

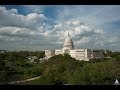
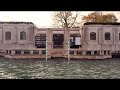
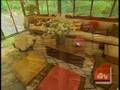
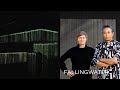
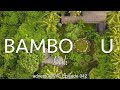

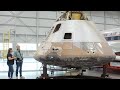
