Carbon Fiber Prepreg PART MAKING (Tutorial) ***PART2***
Hi Everyone and Welcome to PART 2
If you missed PART1 here is the link:
https://youtu.be/pgNNtbixQLo
In this video I explain you all the steps to go from the mould we made in previous tutorial to making prepreg parts in this video.
Full description will follow:
XPREG® XC110 is an advanced out of autoclave prepreg carbon fibre surface system designed specifically for out-of-autoclave (vacuum bag, oven cure) processing. After several years in development, XC110 is a class-leading prepreg system capable of producing carbon fibre components with a 'class A' surface finish and minimal void content when oven-cured under vacuum pressure only.
Components made using the XC110 resin system offer mechanical properties comparable to autoclave-cure systems (such as XPREG® XC130) without the need for expensive autoclave plant or the associated cycle costs. The system is also ideally suited for large components which exceed the capacity of typical autoclaves, such as boat hulls and turbine blades.
XC110 prepregs can be backed-up with (and co-cured alongside) unidirectional reinforcement (from the XC130 range) and are fully compatible with our XA120 adhesive film meaning that even the most complex composite structures - including honeycomb cores - can be achieved out-of-autoclave.
The OOA prepreg carbon fibre 3k 210g material listed on this page is recommended for use as a surface ply, typically backed-up with one or more layers of XC110 450g 12k Backing Ply.
Recommended Uses
OOA prepreg carbon fibre surface fabrics such as this XC110 are the recommended system for both structural and cosmetic applications where components will be cured without an autoclave.
The combination of excellent mechanical performance, visual quality appearance and class-A surface finish make XC110 prepregs suitable for a wide range of applications from large-scale structural components to high-precision cosmetic parts.
Curing
XPREG® XC110 is designed to be oven cured in a vacuum bag at full vacuum pressure however it can also be cured in an autoclave or hot-press. Minimum vacuum pressure is 10mbar.
For best results, an accurately controlled multi-stage temperature cycle with final cure temperature of 120°C should be followed. See technical datasheet or XC110 Processing Guide for details, including a range of alternative cure cycles from 85°C.
Suitable Moulds/Tooling
Moulds/tools should be epoxy-based composite moulds, epoxy tooling board or metal. In all cases, moulds must be temperature stable to a minimum of 85°C but ideally to 120°C.
Fully Compatible:
High temp epoxy hand-layup moulds (e.g. EG160 / EMP160)
Carbon or glass fibre prepreg moulds (e.g. XPREG® XT135)
Epoxy tooling board (e.g. EP700 Epoxy Tooling Board with S120 Board Sealer)
Aluminium / stainless steel moulds
Toughened glass (for flat sheet/panels)
Although it is possible to use vinylester tools (such as Uni-Mould™) they are not recommended due to the increased possibility of surface imperfections (pin holes) which can occur when XPREG® XC110 is cured in the presence of vinylester.
See technical data sheet and XC110 Processing Guide for full details on mould compatibility.
#Carbonfiber #howto #composites #prepreg
Видео Carbon Fiber Prepreg PART MAKING (Tutorial) ***PART2*** канала Matthieu Libeert
If you missed PART1 here is the link:
https://youtu.be/pgNNtbixQLo
In this video I explain you all the steps to go from the mould we made in previous tutorial to making prepreg parts in this video.
Full description will follow:
XPREG® XC110 is an advanced out of autoclave prepreg carbon fibre surface system designed specifically for out-of-autoclave (vacuum bag, oven cure) processing. After several years in development, XC110 is a class-leading prepreg system capable of producing carbon fibre components with a 'class A' surface finish and minimal void content when oven-cured under vacuum pressure only.
Components made using the XC110 resin system offer mechanical properties comparable to autoclave-cure systems (such as XPREG® XC130) without the need for expensive autoclave plant or the associated cycle costs. The system is also ideally suited for large components which exceed the capacity of typical autoclaves, such as boat hulls and turbine blades.
XC110 prepregs can be backed-up with (and co-cured alongside) unidirectional reinforcement (from the XC130 range) and are fully compatible with our XA120 adhesive film meaning that even the most complex composite structures - including honeycomb cores - can be achieved out-of-autoclave.
The OOA prepreg carbon fibre 3k 210g material listed on this page is recommended for use as a surface ply, typically backed-up with one or more layers of XC110 450g 12k Backing Ply.
Recommended Uses
OOA prepreg carbon fibre surface fabrics such as this XC110 are the recommended system for both structural and cosmetic applications where components will be cured without an autoclave.
The combination of excellent mechanical performance, visual quality appearance and class-A surface finish make XC110 prepregs suitable for a wide range of applications from large-scale structural components to high-precision cosmetic parts.
Curing
XPREG® XC110 is designed to be oven cured in a vacuum bag at full vacuum pressure however it can also be cured in an autoclave or hot-press. Minimum vacuum pressure is 10mbar.
For best results, an accurately controlled multi-stage temperature cycle with final cure temperature of 120°C should be followed. See technical datasheet or XC110 Processing Guide for details, including a range of alternative cure cycles from 85°C.
Suitable Moulds/Tooling
Moulds/tools should be epoxy-based composite moulds, epoxy tooling board or metal. In all cases, moulds must be temperature stable to a minimum of 85°C but ideally to 120°C.
Fully Compatible:
High temp epoxy hand-layup moulds (e.g. EG160 / EMP160)
Carbon or glass fibre prepreg moulds (e.g. XPREG® XT135)
Epoxy tooling board (e.g. EP700 Epoxy Tooling Board with S120 Board Sealer)
Aluminium / stainless steel moulds
Toughened glass (for flat sheet/panels)
Although it is possible to use vinylester tools (such as Uni-Mould™) they are not recommended due to the increased possibility of surface imperfections (pin holes) which can occur when XPREG® XC110 is cured in the presence of vinylester.
See technical data sheet and XC110 Processing Guide for full details on mould compatibility.
#Carbonfiber #howto #composites #prepreg
Видео Carbon Fiber Prepreg PART MAKING (Tutorial) ***PART2*** канала Matthieu Libeert
Показать
Комментарии отсутствуют
Информация о видео
Другие видео канала
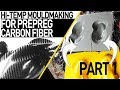
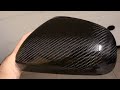
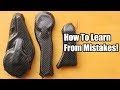



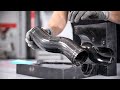
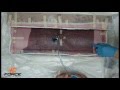
![How to Bake Prepreg Carbon Fiber Brake Cooling Ducts in an Oven [DIY]](https://i.ytimg.com/vi/d3SY8l3jbTo/default.jpg)
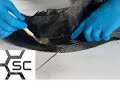
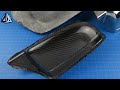
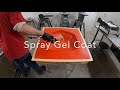
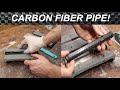
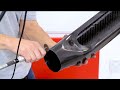
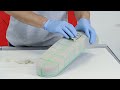
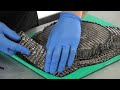
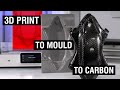
![How to Make a Carbon Fiber Wing [DIY] (with 3D Printed Molds)](https://i.ytimg.com/vi/BSv0XuPGUig/default.jpg)
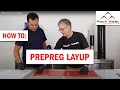
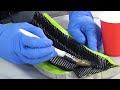