How to Refinish Rusty Fasteners with a Black Oxide Coating
How to refinish rusty bolts with a black oxide coating. This is a chemical process that creates a satin black finish which provides a form of rust protection. The coating is only resistant to moisture, extensive exposure to moisture will eventually cause rust so it’s not applicable for all applications. This is great for any restorations or if you’re having to make some custom hardware as well, it’s not just limited to fasteners either. #rust #restoration #refinishing
Website: http://4diyers.com
Patreon: https://www.patreon.com/4diyers
Facebook: https://www.facebook.com/4diyers
Twitter: https://twitter.com/4DIYers
Instagram: https://www.instagram.com/4diyers/
Tumblr: http://4diyers.tumblr.com
Pintrest: https://www.pinterest.com/4diyers/
Tools/Supplies Needed:
-drill press
-wire wheel
-abrasive pad
-media blaster
-solvent
-black oxide chemical
-paper towel
-WD40
Chapters:
00:00 Intro
00:34 Stripping Rust with Vinegar
01:37 Wire Wheel Cleaning
02:41 Abrasive Pad Cleaning
03:02 Media Blasting Cleaning
03:53 Decontamination
04:20 Black Oxide Chemical
04:45 Dipping the Parts
06:01 Final Finish
Procedure:
One of the easier ways I find detailing with rusty bolts is soaking them in vinegar for a couple of days. This will strip any coatings, paint, and rust. Make sure the hardware is free of any grease or oil which can create a barrier, not allowing the vinegar to do its job. Place the fasteners in a container, something which has a lid will help reduce any evaporation. Make sure they are fully submerged, put the lid in place and then store it somewhere safe for a couple of days. After 12-24 hours, you can shake the container to help agitate the fasteners.
After 48hrs, remove the fasteners and allow any residue on the surface to drip off. They currently have a black oxidized finish, this will need to be removed. I will provide three different finish examples, the first one will be using a wire wheel. This is on a drill press, a bench grinder will work too. You’ll need to make sure that black coating is completely removed, along with any previous plating, paint, and even mill scale depending on the application.
The jar in the background is filled with a wax and grease remover, the parts will soak for a few minutes to remove any oils on the surface which can cause issues in the black oxide coating. When using a wire wheel, also be careful around the threads as you can cause damage.
As the second example, here I’m using an abrasive scotch brite pad, again this is installed in the drill press. This is rated at a 400 grit finish, I have found it gives a slightly more matte finish than compared to the wire wheel which seems to polish the surface. Wire wheels also have various grit ratings, therefore they will leave a different surface finish too.
And as the third example, this would be a media blaster. For this, I’m using a glass bead to clean the part instead of vinegar. This will remove any rust, paint, and coatings without removing any metal material. It leaves a very flat uniform finish.
xa
After those fasteners have been soaking in the solvent, this will remove any contaminants, grease, or even just oil from your skin. Rubber gloves are a must here so the fasteners don’t become contaminated, otherwise they’ll leave imperfections in the surface finish. Each part is wiped down and left on a paper towel to have any remaining solvent evaporate.
The chemical used for black oxide is a concentrate that is required to be mixed with distilled water. The solution is mixed anywhere from 4:1 to 9:1, chemical to water ratio. I ended up mixing it at about 4 parts water to 1 part chemical.
Drop the parts in the solution, it can also be brushed on if you wish. They’ll need to soak for about 5 to 10 minutes.
Mix the solution every couple of minutes to ensure everything is evenly coated. When working with this solution, make sure you are in a well-ventilated area, a mask is recommended as well as rubber gloves.
Once done, using the magnetic screwdriver, remove the fasteners from the solution and rinse them in clean distilled water. Remove from the distilled water and dry off the parts with a paper towel.
Once responsibly dry, the coating needs to be protected from moisture. Oil will need to be applied, this will soak into the coating and provide a layer of protection. Here I have a jar with WD40, let it soak for an hour or more.
Using another magnetized screwdriver, remove the fasteners from the oil and place them on a paper towel, then dry any excessive amount of oil.
Thank you to all those who watch my videos and support my content. Don't forget to subscribe to my channel for future tutorial videos and like my video if you found it helpful. New videos are always being uploaded every week!
© 4DIYers 2013
All Rights Reserved
No part of this video or any of its contents may be reproduced, copied, modified or adapted, without the prior written consent of the author.
Видео How to Refinish Rusty Fasteners with a Black Oxide Coating канала 4DIYers
Website: http://4diyers.com
Patreon: https://www.patreon.com/4diyers
Facebook: https://www.facebook.com/4diyers
Twitter: https://twitter.com/4DIYers
Instagram: https://www.instagram.com/4diyers/
Tumblr: http://4diyers.tumblr.com
Pintrest: https://www.pinterest.com/4diyers/
Tools/Supplies Needed:
-drill press
-wire wheel
-abrasive pad
-media blaster
-solvent
-black oxide chemical
-paper towel
-WD40
Chapters:
00:00 Intro
00:34 Stripping Rust with Vinegar
01:37 Wire Wheel Cleaning
02:41 Abrasive Pad Cleaning
03:02 Media Blasting Cleaning
03:53 Decontamination
04:20 Black Oxide Chemical
04:45 Dipping the Parts
06:01 Final Finish
Procedure:
One of the easier ways I find detailing with rusty bolts is soaking them in vinegar for a couple of days. This will strip any coatings, paint, and rust. Make sure the hardware is free of any grease or oil which can create a barrier, not allowing the vinegar to do its job. Place the fasteners in a container, something which has a lid will help reduce any evaporation. Make sure they are fully submerged, put the lid in place and then store it somewhere safe for a couple of days. After 12-24 hours, you can shake the container to help agitate the fasteners.
After 48hrs, remove the fasteners and allow any residue on the surface to drip off. They currently have a black oxidized finish, this will need to be removed. I will provide three different finish examples, the first one will be using a wire wheel. This is on a drill press, a bench grinder will work too. You’ll need to make sure that black coating is completely removed, along with any previous plating, paint, and even mill scale depending on the application.
The jar in the background is filled with a wax and grease remover, the parts will soak for a few minutes to remove any oils on the surface which can cause issues in the black oxide coating. When using a wire wheel, also be careful around the threads as you can cause damage.
As the second example, here I’m using an abrasive scotch brite pad, again this is installed in the drill press. This is rated at a 400 grit finish, I have found it gives a slightly more matte finish than compared to the wire wheel which seems to polish the surface. Wire wheels also have various grit ratings, therefore they will leave a different surface finish too.
And as the third example, this would be a media blaster. For this, I’m using a glass bead to clean the part instead of vinegar. This will remove any rust, paint, and coatings without removing any metal material. It leaves a very flat uniform finish.
xa
After those fasteners have been soaking in the solvent, this will remove any contaminants, grease, or even just oil from your skin. Rubber gloves are a must here so the fasteners don’t become contaminated, otherwise they’ll leave imperfections in the surface finish. Each part is wiped down and left on a paper towel to have any remaining solvent evaporate.
The chemical used for black oxide is a concentrate that is required to be mixed with distilled water. The solution is mixed anywhere from 4:1 to 9:1, chemical to water ratio. I ended up mixing it at about 4 parts water to 1 part chemical.
Drop the parts in the solution, it can also be brushed on if you wish. They’ll need to soak for about 5 to 10 minutes.
Mix the solution every couple of minutes to ensure everything is evenly coated. When working with this solution, make sure you are in a well-ventilated area, a mask is recommended as well as rubber gloves.
Once done, using the magnetic screwdriver, remove the fasteners from the solution and rinse them in clean distilled water. Remove from the distilled water and dry off the parts with a paper towel.
Once responsibly dry, the coating needs to be protected from moisture. Oil will need to be applied, this will soak into the coating and provide a layer of protection. Here I have a jar with WD40, let it soak for an hour or more.
Using another magnetized screwdriver, remove the fasteners from the oil and place them on a paper towel, then dry any excessive amount of oil.
Thank you to all those who watch my videos and support my content. Don't forget to subscribe to my channel for future tutorial videos and like my video if you found it helpful. New videos are always being uploaded every week!
© 4DIYers 2013
All Rights Reserved
No part of this video or any of its contents may be reproduced, copied, modified or adapted, without the prior written consent of the author.
Видео How to Refinish Rusty Fasteners with a Black Oxide Coating канала 4DIYers
Показать
Комментарии отсутствуют
Информация о видео
Другие видео канала

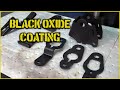
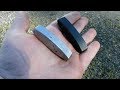
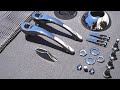
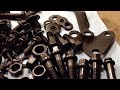
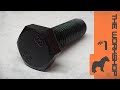


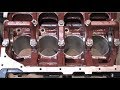
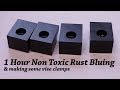
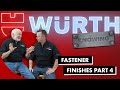
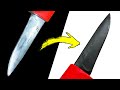
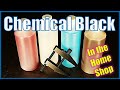
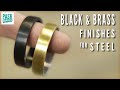

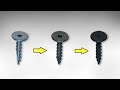
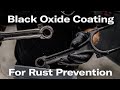
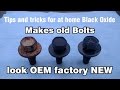
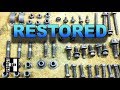
