Six Sigma Green Belt Training Video 2020 Part 1 | Six Sigma Green Belt Tutorial | Lecteron
Six Sigma Green Belt Training Video 2020 Part 1 | Six Sigma Green Belt Tutorial
https://www.lecteron.com/quality-management/lean-six-sigma-green-belt-certification?utm_campaign=ssgb-train-video-part1-vc0IOa1nQX8&utm_medium=YM&utm_source=youtube
Hello and welcome to the Lean Six Sigma Green Belt Training Program organized by Lecteron. This is an instructor-led online training. Lean and Six Sigma are becoming quite popular as the six sigma professionals are in great demand because of their ability to make a significant impact on the business.
So, what is Six Sigma?
It is an approach to achieve customer satisfaction & business excellence through a systematic problem-solving methodology aiming at identifying & reducing the process variation to achieve optimized process variation to achieve process output.
The organization has no choice but to offer the best quality products and services at the minimum cost – which is the purpose and objective of six sigma.
Let’s look into the topics covered in this six sigma green belt training, in this the trainer covers 5 phases of one of the most powerful methodology within lean six sigma, which is called DMAIC.
• Define Quality
• Evolution of Quality
• History of Six Sigma
• Project Methodology
• Six Sigma Vs. Traditional Process Improvement Methods
Elaboration of some important topics in this Six Sigma Green Belt Training Video:
• Sigma is a measurement of quality to know effectively we eliminate defects and variation in a process
• Sigma Level: A measure of process performance (calculated from DPMO)
• DPMO: Defects per million opportunity
• Yield: Defect-free percentage
The focus of Six Sigma:
DMAIC Process:
1. An improvement system for existing processes falling below specification
2. Looking for incremental improvement
DMADV Process:
1. Is an improvement system used to develop new processes or products
2. If a current process requires more than just incremental improvement.
VOC, VOB, VOE:
The foundation of six sigma requires to focus on the voices of the customer, the business and the employee which provides:
Voice of the customer is the customer complaints and suggestions and voice of business is the suggestion of the top management passed on to the belt on increasing the revenue of the company and voice of the employee is the voice of process owner who can be the manager or the production in charge of your company
• Awareness of the needs that are critical to the quality (CTQ) of our products and services
• Identification of the gaps between what is and what should be
• Identification of the process defects that contribute to the gap
• Knowledge of which processes are most broken
• Enlightenment as to the unacceptable Costs of poor Quality (COPO)
Critical to Quality (CTQ): Any measurable product or service characteristics that are important to the customer from the customer’s point of view. A CTQ is a VOC translated into measurable terms.
• What they say (VOC): Your Claims processing is slow and is never right
• What they mean (Translation): I want the claims processed faster, & I want claims to be right
• CTQ (Measurable): Process all claims in 1 o 4 business days, Process all claims accurately the first time
Kano Model: Kano (A Japanese researcher) stated that there are four types of customer needs or reactions to product characteristics/attributes.
1. The ‘Surprise & Delight’ factors. These really make your product stand out from the others. e.g, a passenger jet that could take off vertically.
2. The ‘More is Better’ jet airliner that uses a little less fuel than the competition
3. The ‘must be’ things. Without this, you will never sell the product E.g a jet airliner that cannot meet airport noise regulations
4. Finally there are the ‘dis-satisfiers’ the things that cause your customers not to like your product. E.g a jet airliner that is uncomfortable to ride in.
Goal Statement:
• Definition of improvement the team seeking to accomplish
• Starts with a verb (reduce, eliminate, control, increase)
• Should be realistic and not aggressive
• Transforms vision into a discrete statement of direction
• Should be SMART ( specific, measurable, attainable, relevant, time-bound)
Executive Leadership: Not all Six Sigma deployments are driven from the top by executive leadership. The data is clear, however, that those deployments that are driven by executive management are much more successful than those that are not.
For more information on Six Sigma and other quality management courses, please write in your queries to us at support@lecteron.com or call us at USA: 832-648-7874
#sixsigma #sixsigmaCertification #Lecteron #sixsigmaTrainingvideo
Subscribe to our channel to get more video updates.
Website: https://www.lecteron.com/
Linkedin: https://www.linkedin.com/company/lecteron-solutions-pvt-ltd
Facebook: https://www.facebook.com/Lecteron/
Видео Six Sigma Green Belt Training Video 2020 Part 1 | Six Sigma Green Belt Tutorial | Lecteron канала Lecteron
https://www.lecteron.com/quality-management/lean-six-sigma-green-belt-certification?utm_campaign=ssgb-train-video-part1-vc0IOa1nQX8&utm_medium=YM&utm_source=youtube
Hello and welcome to the Lean Six Sigma Green Belt Training Program organized by Lecteron. This is an instructor-led online training. Lean and Six Sigma are becoming quite popular as the six sigma professionals are in great demand because of their ability to make a significant impact on the business.
So, what is Six Sigma?
It is an approach to achieve customer satisfaction & business excellence through a systematic problem-solving methodology aiming at identifying & reducing the process variation to achieve optimized process variation to achieve process output.
The organization has no choice but to offer the best quality products and services at the minimum cost – which is the purpose and objective of six sigma.
Let’s look into the topics covered in this six sigma green belt training, in this the trainer covers 5 phases of one of the most powerful methodology within lean six sigma, which is called DMAIC.
• Define Quality
• Evolution of Quality
• History of Six Sigma
• Project Methodology
• Six Sigma Vs. Traditional Process Improvement Methods
Elaboration of some important topics in this Six Sigma Green Belt Training Video:
• Sigma is a measurement of quality to know effectively we eliminate defects and variation in a process
• Sigma Level: A measure of process performance (calculated from DPMO)
• DPMO: Defects per million opportunity
• Yield: Defect-free percentage
The focus of Six Sigma:
DMAIC Process:
1. An improvement system for existing processes falling below specification
2. Looking for incremental improvement
DMADV Process:
1. Is an improvement system used to develop new processes or products
2. If a current process requires more than just incremental improvement.
VOC, VOB, VOE:
The foundation of six sigma requires to focus on the voices of the customer, the business and the employee which provides:
Voice of the customer is the customer complaints and suggestions and voice of business is the suggestion of the top management passed on to the belt on increasing the revenue of the company and voice of the employee is the voice of process owner who can be the manager or the production in charge of your company
• Awareness of the needs that are critical to the quality (CTQ) of our products and services
• Identification of the gaps between what is and what should be
• Identification of the process defects that contribute to the gap
• Knowledge of which processes are most broken
• Enlightenment as to the unacceptable Costs of poor Quality (COPO)
Critical to Quality (CTQ): Any measurable product or service characteristics that are important to the customer from the customer’s point of view. A CTQ is a VOC translated into measurable terms.
• What they say (VOC): Your Claims processing is slow and is never right
• What they mean (Translation): I want the claims processed faster, & I want claims to be right
• CTQ (Measurable): Process all claims in 1 o 4 business days, Process all claims accurately the first time
Kano Model: Kano (A Japanese researcher) stated that there are four types of customer needs or reactions to product characteristics/attributes.
1. The ‘Surprise & Delight’ factors. These really make your product stand out from the others. e.g, a passenger jet that could take off vertically.
2. The ‘More is Better’ jet airliner that uses a little less fuel than the competition
3. The ‘must be’ things. Without this, you will never sell the product E.g a jet airliner that cannot meet airport noise regulations
4. Finally there are the ‘dis-satisfiers’ the things that cause your customers not to like your product. E.g a jet airliner that is uncomfortable to ride in.
Goal Statement:
• Definition of improvement the team seeking to accomplish
• Starts with a verb (reduce, eliminate, control, increase)
• Should be realistic and not aggressive
• Transforms vision into a discrete statement of direction
• Should be SMART ( specific, measurable, attainable, relevant, time-bound)
Executive Leadership: Not all Six Sigma deployments are driven from the top by executive leadership. The data is clear, however, that those deployments that are driven by executive management are much more successful than those that are not.
For more information on Six Sigma and other quality management courses, please write in your queries to us at support@lecteron.com or call us at USA: 832-648-7874
#sixsigma #sixsigmaCertification #Lecteron #sixsigmaTrainingvideo
Subscribe to our channel to get more video updates.
Website: https://www.lecteron.com/
Linkedin: https://www.linkedin.com/company/lecteron-solutions-pvt-ltd
Facebook: https://www.facebook.com/Lecteron/
Видео Six Sigma Green Belt Training Video 2020 Part 1 | Six Sigma Green Belt Tutorial | Lecteron канала Lecteron
Показать
Комментарии отсутствуют
Информация о видео
Другие видео канала

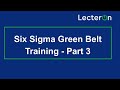


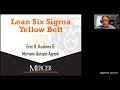
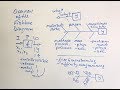
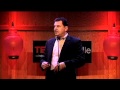
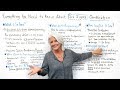
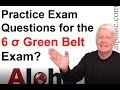
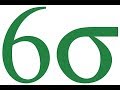
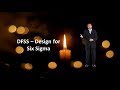

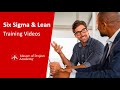
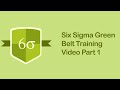


![Introduction to Six Sigma [ Explained in 10 Minutes ]](https://i.ytimg.com/vi/wEBPVQ7W2wg/default.jpg)
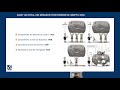

