Bench test of quenching oil composite additives. Please contact us for more information.
The main purpose of the bench test of quenching oil composite additives is to verify the performance of additives under conditions close to actual application, including cooling characteristics, antioxidant stability, thermal stability, cleanliness and anti-corrosion performance. Bench test is an important bridge from laboratory to industrial application, and its results are of guiding significance for the improvement and optimization of composite additives.
1. Experimental purpose
Verify cooling performance: Test the cooling curve of quenching oil to ensure that it meets the requirements of metal quenching process.
Evaluate antioxidant and thermal stability: Verify the stability of quenching oil under high temperature and long-term use.
Test metal surface anti-corrosion performance: Test the protective effect of quenching oil on workpieces and equipment.
Verify cleaning performance: Evaluate the formation of sludge, varnish and carbon deposits.
Oil life test: Evaluate the service life of quenching oil in actual use.
2. Experimental equipment and instruments
(1) Cooling performance test equipment
Cooling curve meter: Test the cooling rate of oil on standard workpieces.
Common instruments: Cooling rate analyzer (such as IVF cooling curve meter).
(2) Thermal stability test equipment
Thermal oxidation acceleration tester:
Simulates the oxidation process of oil products under high temperature conditions.
Common method: ASTM D943 (determination of oil product oxidation life).
(3) Cleaning performance test equipment
Thermal decomposition tester:
Tests whether oil products form deposits under high temperature conditions.
Test standard: DIN 51585 (evaluation of thermal oxidation stability of quenching oil).
(4) Corrosion resistance test equipment
Corrosion immersion test bench:
Tests the corrosion resistance of oil products to different metal materials (such as steel, copper, and aluminum).
Common standards: ASTM D665 (rust resistance of steel) and ASTM D130 (corrosion of copper sheets).
(5) Cyclic use simulation equipment
Industrial simulated quenching equipment:
Simulates the cyclic use performance of oil products under actual quenching conditions.
3. Experimental methods and steps
(1) Cooling performance test
Steps:
Select a standard specimen (such as a metal bar or workpiece).
Heat the specimen to a specified temperature (800-1000°C) and then immerse it in quenching oil.
The temperature change is recorded by the cooling curve instrument and the cooling curve is drawn.
Evaluation indicators:
Initial cooling speed (cooling rate in high temperature zone).
Cooling uniformity (smoothness of cooling rate curve).
Temperature control in the post-cooling stage (to prevent cracking).
(2) Thermal oxidation stability test
Steps:
Place the oil sample in the thermal oxidation test instrument and heat it at a specified high temperature (150-200°C) for a certain time.
Take samples at regular intervals to analyze the acid value (TAN) and viscosity changes.
Evaluation indicators:
Oxidation stability (acid value growth rate).
Viscosity change rate.
Amount of deposits formed.
(3) Anti-corrosion test
Steps:
Immerse the metal sheet (such as steel sheet, copper sheet) in the oil sample and maintain a certain temperature (60-80°C) and time (24-72 hours).
Take out the metal sheet, clean it, and observe the surface changes.
Use an optical microscope or scanning electron microscope (SEM) to detect the degree of corrosion.
Evaluation indicators:
Corrosion level (in accordance with ASTM D130 or D665).
Number and distribution of surface spots.
(4) Cleanliness test
Steps:
Keep the oil sample at high temperature for a certain period of time (such as 300°C, 4 hours).
Observe the color and amount of sediment of the oil sample.
Use Fourier transform infrared spectroscopy (FTIR) or thermogravimetric analysis (TGA) to analyze the decomposition products of the oil.
Evaluation indicators:
The amount of sludge and carbon deposits generated.
Oil cleanliness.
(5) Cyclic performance test
Steps:
Use simulated quenching equipment to set cyclic heating and cooling conditions.
Record the performance changes of the oil after multiple cycles, including cooling rate, viscosity and acid value.
Compare the oil performance indicators before and after the experiment.
Evaluation indicators:
Cooling curve stability.
Viscosity and acid value change rate.
Oil life (number of uses or time).
4. Experimental data analysis and result evaluation
(1) Data analysis
Cooling curve comparison: whether it meets the process requirements.
Oxidation and corrosion indicators: whether the antioxidant and preservative are effective.
Deposit analysis: the effect of detergent and high temperature stabilizer.
(2) Decision-making based on experimental results
If a certain performance does not meet the standard:
Adjust the additive ratio.
Change the base oil type.
Improve specific functional additives (such as antioxidants or detergents).
Видео Bench test of quenching oil composite additives. Please contact us for more information. канала Minglan Shanghai
oil additive, minglan, Lubricant Additive, Engine Oil Additive, Gear Oil Additive, Hydraulic Oil Additive, Industrial Oil Additive
1. Experimental purpose
Verify cooling performance: Test the cooling curve of quenching oil to ensure that it meets the requirements of metal quenching process.
Evaluate antioxidant and thermal stability: Verify the stability of quenching oil under high temperature and long-term use.
Test metal surface anti-corrosion performance: Test the protective effect of quenching oil on workpieces and equipment.
Verify cleaning performance: Evaluate the formation of sludge, varnish and carbon deposits.
Oil life test: Evaluate the service life of quenching oil in actual use.
2. Experimental equipment and instruments
(1) Cooling performance test equipment
Cooling curve meter: Test the cooling rate of oil on standard workpieces.
Common instruments: Cooling rate analyzer (such as IVF cooling curve meter).
(2) Thermal stability test equipment
Thermal oxidation acceleration tester:
Simulates the oxidation process of oil products under high temperature conditions.
Common method: ASTM D943 (determination of oil product oxidation life).
(3) Cleaning performance test equipment
Thermal decomposition tester:
Tests whether oil products form deposits under high temperature conditions.
Test standard: DIN 51585 (evaluation of thermal oxidation stability of quenching oil).
(4) Corrosion resistance test equipment
Corrosion immersion test bench:
Tests the corrosion resistance of oil products to different metal materials (such as steel, copper, and aluminum).
Common standards: ASTM D665 (rust resistance of steel) and ASTM D130 (corrosion of copper sheets).
(5) Cyclic use simulation equipment
Industrial simulated quenching equipment:
Simulates the cyclic use performance of oil products under actual quenching conditions.
3. Experimental methods and steps
(1) Cooling performance test
Steps:
Select a standard specimen (such as a metal bar or workpiece).
Heat the specimen to a specified temperature (800-1000°C) and then immerse it in quenching oil.
The temperature change is recorded by the cooling curve instrument and the cooling curve is drawn.
Evaluation indicators:
Initial cooling speed (cooling rate in high temperature zone).
Cooling uniformity (smoothness of cooling rate curve).
Temperature control in the post-cooling stage (to prevent cracking).
(2) Thermal oxidation stability test
Steps:
Place the oil sample in the thermal oxidation test instrument and heat it at a specified high temperature (150-200°C) for a certain time.
Take samples at regular intervals to analyze the acid value (TAN) and viscosity changes.
Evaluation indicators:
Oxidation stability (acid value growth rate).
Viscosity change rate.
Amount of deposits formed.
(3) Anti-corrosion test
Steps:
Immerse the metal sheet (such as steel sheet, copper sheet) in the oil sample and maintain a certain temperature (60-80°C) and time (24-72 hours).
Take out the metal sheet, clean it, and observe the surface changes.
Use an optical microscope or scanning electron microscope (SEM) to detect the degree of corrosion.
Evaluation indicators:
Corrosion level (in accordance with ASTM D130 or D665).
Number and distribution of surface spots.
(4) Cleanliness test
Steps:
Keep the oil sample at high temperature for a certain period of time (such as 300°C, 4 hours).
Observe the color and amount of sediment of the oil sample.
Use Fourier transform infrared spectroscopy (FTIR) or thermogravimetric analysis (TGA) to analyze the decomposition products of the oil.
Evaluation indicators:
The amount of sludge and carbon deposits generated.
Oil cleanliness.
(5) Cyclic performance test
Steps:
Use simulated quenching equipment to set cyclic heating and cooling conditions.
Record the performance changes of the oil after multiple cycles, including cooling rate, viscosity and acid value.
Compare the oil performance indicators before and after the experiment.
Evaluation indicators:
Cooling curve stability.
Viscosity and acid value change rate.
Oil life (number of uses or time).
4. Experimental data analysis and result evaluation
(1) Data analysis
Cooling curve comparison: whether it meets the process requirements.
Oxidation and corrosion indicators: whether the antioxidant and preservative are effective.
Deposit analysis: the effect of detergent and high temperature stabilizer.
(2) Decision-making based on experimental results
If a certain performance does not meet the standard:
Adjust the additive ratio.
Change the base oil type.
Improve specific functional additives (such as antioxidants or detergents).
Видео Bench test of quenching oil composite additives. Please contact us for more information. канала Minglan Shanghai
oil additive, minglan, Lubricant Additive, Engine Oil Additive, Gear Oil Additive, Hydraulic Oil Additive, Industrial Oil Additive
Показать
Комментарии отсутствуют
Информация о видео
27 декабря 2024 г. 6:39:21
00:00:08
Другие видео канала
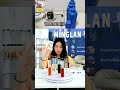

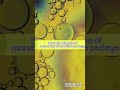
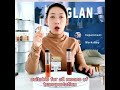

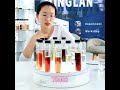
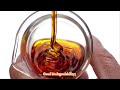

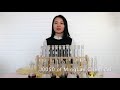

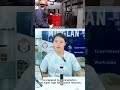


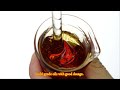



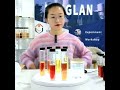

