The Story of Welding
For thousands of years, bonding or joining metals has been deep-rooted in the history of human civilization; as far as the Bronze and Iron Age in Europe and the Middle East. One of the earliest examples came from the construction of the Iron pillar of Delhi, erected in Delhi, India about 310 AD. The Iron pillar of Delhi weighs an astonishing 5.4 metric tons and is famous for the rust-resistant composition of the alloys used in its creation. According to archeologists, the pillar is a “testimony to the high level of skill achieved by the ancient Indian iron smiths in the extraction and processing of iron."
As civilization transitioned into the middle ages, further advancements in forge welding began to surface. Forge welding is a solid-state process in which two pieces of metal are merged by heating them to temperatures high enough that result in plastic deformation and then striking or pressing them together. This was accomplished by blacksmiths who repeatedly hammered heated metal until bonding occurred. Moreover, this process is the simplest way in which the early civilizations joined metals.
Further, into the renaissance period, craftsmen skilled in the process refined their proficiency and the industry progressed and saw growth in the centuries to come.
By the 1800s, the discovery of the “short pulse” electrical arc was founded by Sir Humphry Davy who presented his results the following year. An arc was generated and suspended in the air between two carbon electrodes using a battery. The illumination produced from the arc was credited as the first practical electric light and was widely used as lighting for streets and large buildings in the 1870s. But, only to be superseded by incandescent lighting by the early 20th century.
Two years after Davy’s discovery, the continuous electric arc was created by Vasily Petrov, a Russian scientist. The following year, he published the results of his experiments and the significance of prolonged electrical discharge or stable arc discharge. In his paper, Petrov emphasized its use for a multitude of applications, especially for melting metals.
In 1881 the first electric arc welding method was created by inventors Nikolai Benardos and Stanisław Olszewski, known as carbon arc welding. With this method, carbon electrodes are used to generate an electric arc between the electrode itself and the base materials. The temperatures produced were high enough to form a bond between separate metals that eventually become welded.
By the late 1800s, arc welding saw further advancements with the invention of metal electrodes pioneered by Russan inventor Nikolai Slavyanov and American engineer C. L. Coffin. Metal electrodes later improved around the 1900s with the development of a metal-mixture coating called flux. The flux would give off gases as it decomposed to prevent weld contamination. This new design was accredited to British scientist A. P. Strohmenger which gave a more stable arc and improved the weld quality.
As the 20th century progressed, a plethora of welding methods such as resistance welding, thermite welding, and oxyfuel welding was developed but, fell out of favor for industrial applications. They were largely replaced with arc welding, as headway was made in the advancements of flux. The benefit of flux coating the electrode is the gas shield it creates to protect the base material from impurities.
During World War I, welding saw a shift in demand as military powers used it in the construction of their fleets. The British army primarily used arc welding, and to an extent, to construct the hull of some of their ships. Arc weldings applications extended to the construction of aircraft for the first time during the war. In fact, some German fuselages were even constructed using this process.
The 1920s then saw the introduction of automatic welding in which spooled electrode wire was fed continuously. But the biggest hurdle was how to protect welds from the effects of oxygen and nitrogen in the atmosphere, which lead to issues with porosity and brittleness. This prompted the next breakthrough in welding technology with the use of shielding gas. Some of the solutions included the use of hydrogen, argon, and helium gas as a welding atmosphere to insulate the base materials.
The following decades saw additional improvements in the welding of reactive metals like aluminum and magnesium which fed a major expansion of arc welding during the 1930s and World War II.
Now that we have a better understanding of some of the history of arc welding. Let’s dive further into the process itself.
The fundamental idea of arc welding is to utilize electricity to generate enough heat in which metal reaches its melting point. The manipulation of the molten metal at the welding region can then be used to bond the base metal with other metals as cooling takes place.
Видео The Story of Welding канала Gear Quest
As civilization transitioned into the middle ages, further advancements in forge welding began to surface. Forge welding is a solid-state process in which two pieces of metal are merged by heating them to temperatures high enough that result in plastic deformation and then striking or pressing them together. This was accomplished by blacksmiths who repeatedly hammered heated metal until bonding occurred. Moreover, this process is the simplest way in which the early civilizations joined metals.
Further, into the renaissance period, craftsmen skilled in the process refined their proficiency and the industry progressed and saw growth in the centuries to come.
By the 1800s, the discovery of the “short pulse” electrical arc was founded by Sir Humphry Davy who presented his results the following year. An arc was generated and suspended in the air between two carbon electrodes using a battery. The illumination produced from the arc was credited as the first practical electric light and was widely used as lighting for streets and large buildings in the 1870s. But, only to be superseded by incandescent lighting by the early 20th century.
Two years after Davy’s discovery, the continuous electric arc was created by Vasily Petrov, a Russian scientist. The following year, he published the results of his experiments and the significance of prolonged electrical discharge or stable arc discharge. In his paper, Petrov emphasized its use for a multitude of applications, especially for melting metals.
In 1881 the first electric arc welding method was created by inventors Nikolai Benardos and Stanisław Olszewski, known as carbon arc welding. With this method, carbon electrodes are used to generate an electric arc between the electrode itself and the base materials. The temperatures produced were high enough to form a bond between separate metals that eventually become welded.
By the late 1800s, arc welding saw further advancements with the invention of metal electrodes pioneered by Russan inventor Nikolai Slavyanov and American engineer C. L. Coffin. Metal electrodes later improved around the 1900s with the development of a metal-mixture coating called flux. The flux would give off gases as it decomposed to prevent weld contamination. This new design was accredited to British scientist A. P. Strohmenger which gave a more stable arc and improved the weld quality.
As the 20th century progressed, a plethora of welding methods such as resistance welding, thermite welding, and oxyfuel welding was developed but, fell out of favor for industrial applications. They were largely replaced with arc welding, as headway was made in the advancements of flux. The benefit of flux coating the electrode is the gas shield it creates to protect the base material from impurities.
During World War I, welding saw a shift in demand as military powers used it in the construction of their fleets. The British army primarily used arc welding, and to an extent, to construct the hull of some of their ships. Arc weldings applications extended to the construction of aircraft for the first time during the war. In fact, some German fuselages were even constructed using this process.
The 1920s then saw the introduction of automatic welding in which spooled electrode wire was fed continuously. But the biggest hurdle was how to protect welds from the effects of oxygen and nitrogen in the atmosphere, which lead to issues with porosity and brittleness. This prompted the next breakthrough in welding technology with the use of shielding gas. Some of the solutions included the use of hydrogen, argon, and helium gas as a welding atmosphere to insulate the base materials.
The following decades saw additional improvements in the welding of reactive metals like aluminum and magnesium which fed a major expansion of arc welding during the 1930s and World War II.
Now that we have a better understanding of some of the history of arc welding. Let’s dive further into the process itself.
The fundamental idea of arc welding is to utilize electricity to generate enough heat in which metal reaches its melting point. The manipulation of the molten metal at the welding region can then be used to bond the base metal with other metals as cooling takes place.
Видео The Story of Welding канала Gear Quest
Показать
Комментарии отсутствуют
Информация о видео
Другие видео канала
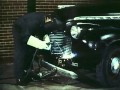
![The Science Of Small Distances [Anniversary Remake]](https://i.ytimg.com/vi/Aw-xbs8ZWxE/default.jpg)
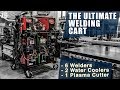
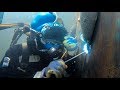

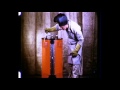
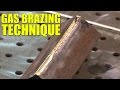
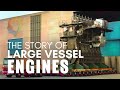
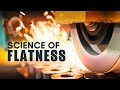
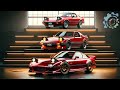
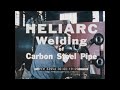
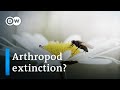
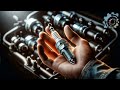
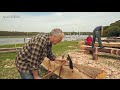
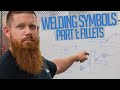
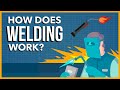

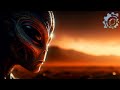

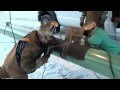