Aerated Concrete Blocks Production Plant - GRIVAS
SELLING DRAWINGS and technical documentation is possible. Contact details: info@grivas.ua, WhatsApp +380681943333
The presentation of the “Prof AC” semiautomatic conveyor-type line for producing aerated concrete blocks. The estimated productivity of the line is 70 cub.m per shift. This video presents the production process of aerated concrete blocks using “Prof AC”. Producing aerated concrete blocks starts with mechanized supplying and automated dosing of fill materials to produce aerated concrete. Having been dosed, the components and water are loaded and mixed in a mixer-activator. Preparing an aluminum suspension and preparing cement-sand mortar are carried out simultaneously. The aluminum suspension is the last component that is loaded into the mixer-activator. Once the aluminum suspension has entered into a chemical reaction, the aerated concrete is poured into a metallic mold, which is transported to a heating chamber where aerated concrete mixture rises and gains the initial strength. After curing for 3-4 hours, the monolith in the mold is supplied to a cutting area where mold’s sides are mechanically removed and the aerated concrete monolith is cut into blocks. The cut blocks are transported on the trolley to a chamber to get a warehouse strength. Gaining the required strength, the blocks are supplied to a packaging area for palletizing and packing blocks onto a transporting pallet. Samples of aerated concrete blocks, which have been selected during production process, are tested at the lab to certify the conformity of a finished product with construction rules and standards. An accurate geometry of aerated concrete blocks allows to build walls using adhesive layer of 3mm.
Subtitles:
0:12 - Presentation of the “Prof AC” semi-automated conveyor-type line for producing aerated concrete blocks
0:12 - The estimated productivity of the line is 70 m3/shift
0:13 - The area for preparing and supplying raw materials to produce aerated concrete
0:15 - The cement silo with an aeration system
0:19 - Mechanized discharger for flexible containers “Big-Bags”
0:29 - The screw conveyor for loading dry mix into a dosing complex
0:48 - The area for preparing aerated concrete
0:51 - Preparing the aluminum suspension
1:05 - Loading and automatically dosing the components to produce aerated concrete
1:09 - Loading all components into the mixer-activator to produce aerated concrete
1:15 - Mixing components in the mixer-activator “GRBU-1500” for two minutes
1:22 - Manual loading of the last component – aluminum powder - to produce aerated concrete
1:28 - Activating aerated concrete mixture within 60 seconds
1:37 - Aerated concrete is being poured into the mold where it rises up to the mold’s volume
1:54 - The mold filled with aerated concrete is being transported to a heating and curing chamber
1:58 - Transverse transportation of the mold can be mechanized by means of installing additional electromechanical pushers
2:26 - The electromechanical pusher moves molds inside of the heating and curing chambers
2:32 - System of limit switches stops and reverts the pusher to its initial position
2:40 - Internal temperature of the curing chambers is controlled with sensors and controllers.
2:52 - The ventilation and heating system of aerated concrete curing chambers
2:58 - Transporting the cured aerated concrete to the cutting area
3:18 - Preparing and removing the framework by means of a gripper
4:11 - Transporting the mold’s sides to the cleaning and assembling area
4:25 - Clearing the mold’s sides from aerated concrete wastes
4:46 - The mold’s sides are installed on the pallet trolley
4:59 - The aerated concrete monolith is trimmed with the machine “UTL-600M” equipped with an electromechanical system to push trolleys
5:04 - The monolith is trimmed on top and bottom sides
5:36 - The aerated concrete monolith is cut into workpieces
5:43 - The cutting area is equipped with a cleaning system to clear the working area from aerated concrete cuttings
6:01 - Cutting the monolith into blocks
6:18 - The aerated concrete monolith, which is cut into blocks, is transported to the curing and maturing chamber to get the strength required for warehousing
7:19 - The cutting area is cleared from aerated concrete cuttings
7:25 - The cuttings can be processed and crushed for reusing
Видео Aerated Concrete Blocks Production Plant - GRIVAS канала GRIVAS Ukraine
The presentation of the “Prof AC” semiautomatic conveyor-type line for producing aerated concrete blocks. The estimated productivity of the line is 70 cub.m per shift. This video presents the production process of aerated concrete blocks using “Prof AC”. Producing aerated concrete blocks starts with mechanized supplying and automated dosing of fill materials to produce aerated concrete. Having been dosed, the components and water are loaded and mixed in a mixer-activator. Preparing an aluminum suspension and preparing cement-sand mortar are carried out simultaneously. The aluminum suspension is the last component that is loaded into the mixer-activator. Once the aluminum suspension has entered into a chemical reaction, the aerated concrete is poured into a metallic mold, which is transported to a heating chamber where aerated concrete mixture rises and gains the initial strength. After curing for 3-4 hours, the monolith in the mold is supplied to a cutting area where mold’s sides are mechanically removed and the aerated concrete monolith is cut into blocks. The cut blocks are transported on the trolley to a chamber to get a warehouse strength. Gaining the required strength, the blocks are supplied to a packaging area for palletizing and packing blocks onto a transporting pallet. Samples of aerated concrete blocks, which have been selected during production process, are tested at the lab to certify the conformity of a finished product with construction rules and standards. An accurate geometry of aerated concrete blocks allows to build walls using adhesive layer of 3mm.
Subtitles:
0:12 - Presentation of the “Prof AC” semi-automated conveyor-type line for producing aerated concrete blocks
0:12 - The estimated productivity of the line is 70 m3/shift
0:13 - The area for preparing and supplying raw materials to produce aerated concrete
0:15 - The cement silo with an aeration system
0:19 - Mechanized discharger for flexible containers “Big-Bags”
0:29 - The screw conveyor for loading dry mix into a dosing complex
0:48 - The area for preparing aerated concrete
0:51 - Preparing the aluminum suspension
1:05 - Loading and automatically dosing the components to produce aerated concrete
1:09 - Loading all components into the mixer-activator to produce aerated concrete
1:15 - Mixing components in the mixer-activator “GRBU-1500” for two minutes
1:22 - Manual loading of the last component – aluminum powder - to produce aerated concrete
1:28 - Activating aerated concrete mixture within 60 seconds
1:37 - Aerated concrete is being poured into the mold where it rises up to the mold’s volume
1:54 - The mold filled with aerated concrete is being transported to a heating and curing chamber
1:58 - Transverse transportation of the mold can be mechanized by means of installing additional electromechanical pushers
2:26 - The electromechanical pusher moves molds inside of the heating and curing chambers
2:32 - System of limit switches stops and reverts the pusher to its initial position
2:40 - Internal temperature of the curing chambers is controlled with sensors and controllers.
2:52 - The ventilation and heating system of aerated concrete curing chambers
2:58 - Transporting the cured aerated concrete to the cutting area
3:18 - Preparing and removing the framework by means of a gripper
4:11 - Transporting the mold’s sides to the cleaning and assembling area
4:25 - Clearing the mold’s sides from aerated concrete wastes
4:46 - The mold’s sides are installed on the pallet trolley
4:59 - The aerated concrete monolith is trimmed with the machine “UTL-600M” equipped with an electromechanical system to push trolleys
5:04 - The monolith is trimmed on top and bottom sides
5:36 - The aerated concrete monolith is cut into workpieces
5:43 - The cutting area is equipped with a cleaning system to clear the working area from aerated concrete cuttings
6:01 - Cutting the monolith into blocks
6:18 - The aerated concrete monolith, which is cut into blocks, is transported to the curing and maturing chamber to get the strength required for warehousing
7:19 - The cutting area is cleared from aerated concrete cuttings
7:25 - The cuttings can be processed and crushed for reusing
Видео Aerated Concrete Blocks Production Plant - GRIVAS канала GRIVAS Ukraine
Показать
Комментарии отсутствуют
Информация о видео
Другие видео канала

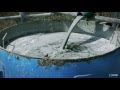
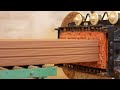
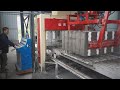

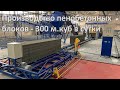

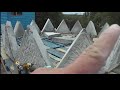
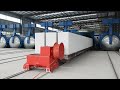
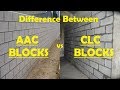
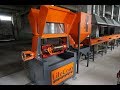
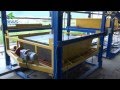


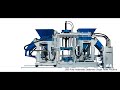
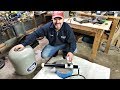
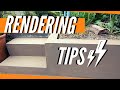
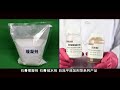
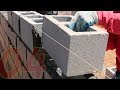
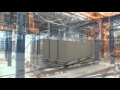