Innovative Human-Robot Collaboration for BMW/MINI Crash Can Assembly
This cell was designed to assist a human operator in reducing repetitive, non-ergonomic tasks that historically required fully manual assembly for the crash can structure located at the front of a BMW/MINI vehicle. Not only did the cell improve ergonomics, it also reduced overall cycle time for the operation.
This particular part is assembled from a combination of three aluminium extrusions, four pop rivets and a number of plastic clips.
In the past operators were required to complete all of these actions within a short time cycle. Moreover the process of securing the pop rivets was one that was not ergonomic for a human to complete as a continual process.
With this in mind the natural solution was to implement a collaborative robot cell, utilizing KUKA technology, allowing for a process to be developed where an operator could fully collaborate with the robot in close proximity.
The robot secures the first two rivets while the operator places the plastic clips into the extrusions on one side. The automated and manual process times balance, so the robot finish at the same time and switch positions to work on opposite sides securing rivets and placing clips.
The cell is fully linked to BMW's production system inside the factory and reports its status, number of rivets fixed etc. back to the engineers running the facility.
Видео Innovative Human-Robot Collaboration for BMW/MINI Crash Can Assembly канала KUKA - Robots & Automation
This particular part is assembled from a combination of three aluminium extrusions, four pop rivets and a number of plastic clips.
In the past operators were required to complete all of these actions within a short time cycle. Moreover the process of securing the pop rivets was one that was not ergonomic for a human to complete as a continual process.
With this in mind the natural solution was to implement a collaborative robot cell, utilizing KUKA technology, allowing for a process to be developed where an operator could fully collaborate with the robot in close proximity.
The robot secures the first two rivets while the operator places the plastic clips into the extrusions on one side. The automated and manual process times balance, so the robot finish at the same time and switch positions to work on opposite sides securing rivets and placing clips.
The cell is fully linked to BMW's production system inside the factory and reports its status, number of rivets fixed etc. back to the engineers running the facility.
Видео Innovative Human-Robot Collaboration for BMW/MINI Crash Can Assembly канала KUKA - Robots & Automation
Показать
Комментарии отсутствуют
Информация о видео
7 марта 2018 г. 19:29:59
00:02:26
Другие видео канала
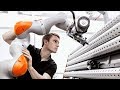
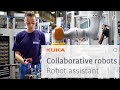


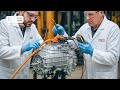
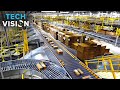
![COBOTS enables Xiamen Runner Industrial Corporation to achieve flexible manufacturing [2020]](https://i.ytimg.com/vi/PtncirKiBXQ/default.jpg)
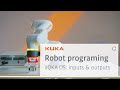
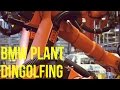


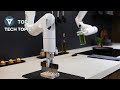
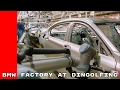
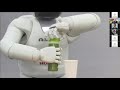
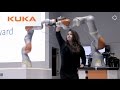
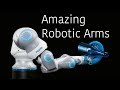
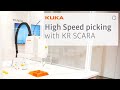
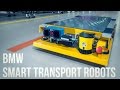

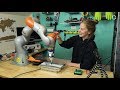