Impact of Airflow on Refrigerant Measurements and Performance
In this class, Bryan teaches the Kalos techs about airflow and how it impacts system performance. He explains the factors that affect airflow and how those contribute to the overall state of an HVAC system. We use training equipment and MeasureQuick to demonstrate these concepts.
On a typical no-cooling call, many techs start with a visual inspection to look for restrictions. These techs will likely check the cleanliness of the filter, blower wheel, and evaporator coil inlet. Some techs also check the return grille, as it may be dirty or have an extra filter. Frozen evaporator coils are also a symptom of poor airflow (frozen evaporator coils also cause even worse airflow).
On the auditory side of inspection, listening for abnormal motor sounds can clue you in on the static pressure, especially when high static pressure affects ECM motors. Alternatively, strange motor noises can tell you about the motor or blower wheel’s health. For example, PSC motors won’t ramp up under high static pressure; abnormal noises indicate bearing wear or a loose hub on the blower wheel.
Customers may cause low airflow in their HVAC systems. For example, customers may close supply air vents to force more air into another room. (To force more air into rooms effectively, an HVAC contractor can cut a duct board so that it flexes and has a small hole, and then they’d insert it into the supply duct to act as a secondary damper. However, this practice may increase static pressure along the way and negatively affect airflow.) Customers may also move furniture in front of the return and obstruct airflow. Pet hair can also plug returns and filters.
Other causes of poor airflow include collapsed or disconnected ducts. Insulation in the unit can also suck up against the blower. (Don’t pull panels off while the unit is running to avoid letting the insulation cause a restriction.) Water in the return can also cause airflow restrictions, especially in flex duct systems. Fire dampers may cause poor airflow in commercial applications. Slipping belts or poorly adjusted sheaves can also contribute to poor airflow.
Before taking any measurements, make sure your gauges have been zeroed out and calibrated against each other. When you have poor airflow, your typical measurements will be either normal or low. You can expect your superheat to be normal to low. Your suction pressure, head pressure, and delta T will also be low. Static pressure is NOT a measure of airflow, but it can tell you about the airflow; you can have poor airflow if the static pressure is good, but the motor may not be producing enough airflow. However, the ULTIMATE indicator of low airflow is a low suction line temperature; any suction line temperature lower than 50 degrees (F) with normal indoor temperature is a likely indication of low airflow.
Some tools that measure airflow include TrueFlow grids, vane anemometers, and hot wire anemometers. However, these are advanced tools, and each one has its limitations. So, the best way to spot a system airflow problem is to perform those inspections with your senses and take your standard measurements.
As air moves over the evaporator coil, it comes into contact with the fins. Heat moves from the air to those fins, as heat moves from warm air to the colder fins. That heat transfer is critical for moving heat from a space, and fins help the evaporator maintain pressure.
When you have low airflow, the compressor amp draw will drop. The reduced pressure indicates that the refrigerant has less mass. The compressor does less work, but it doesn’t get cooled off as easily, and flooding is also possible.
In our class, we used the training equipment to simulate various low-airflow conditions. We also used the MeasureQuick app to profile the equipment, determine our ideal measurement ranges, and display our data. The MeasureQuick app determined that our superheat was hunting and that we were overfeeding our evaporator.
After troubleshooting the unit, we reduced our supply airflow. Our suction line pressure sharply decreased. We then jammed cardboard in the return duct, and our TESP sharply increased. Overall, our suction line temperature decreased sharply, TESP increased sharply, and subcooling increased slightly. MeasureQuick determined that we were running 249 CFM per ton, which indicates very low airflow.
Check out information on the 2022 HVACR Training Symposium at https://hvacrschool.com/symposium/.
Read all the tech tips, take the quizzes, and find our handy calculators at https://www.hvacrschool.com/.
Видео Impact of Airflow on Refrigerant Measurements and Performance канала HVAC School
On a typical no-cooling call, many techs start with a visual inspection to look for restrictions. These techs will likely check the cleanliness of the filter, blower wheel, and evaporator coil inlet. Some techs also check the return grille, as it may be dirty or have an extra filter. Frozen evaporator coils are also a symptom of poor airflow (frozen evaporator coils also cause even worse airflow).
On the auditory side of inspection, listening for abnormal motor sounds can clue you in on the static pressure, especially when high static pressure affects ECM motors. Alternatively, strange motor noises can tell you about the motor or blower wheel’s health. For example, PSC motors won’t ramp up under high static pressure; abnormal noises indicate bearing wear or a loose hub on the blower wheel.
Customers may cause low airflow in their HVAC systems. For example, customers may close supply air vents to force more air into another room. (To force more air into rooms effectively, an HVAC contractor can cut a duct board so that it flexes and has a small hole, and then they’d insert it into the supply duct to act as a secondary damper. However, this practice may increase static pressure along the way and negatively affect airflow.) Customers may also move furniture in front of the return and obstruct airflow. Pet hair can also plug returns and filters.
Other causes of poor airflow include collapsed or disconnected ducts. Insulation in the unit can also suck up against the blower. (Don’t pull panels off while the unit is running to avoid letting the insulation cause a restriction.) Water in the return can also cause airflow restrictions, especially in flex duct systems. Fire dampers may cause poor airflow in commercial applications. Slipping belts or poorly adjusted sheaves can also contribute to poor airflow.
Before taking any measurements, make sure your gauges have been zeroed out and calibrated against each other. When you have poor airflow, your typical measurements will be either normal or low. You can expect your superheat to be normal to low. Your suction pressure, head pressure, and delta T will also be low. Static pressure is NOT a measure of airflow, but it can tell you about the airflow; you can have poor airflow if the static pressure is good, but the motor may not be producing enough airflow. However, the ULTIMATE indicator of low airflow is a low suction line temperature; any suction line temperature lower than 50 degrees (F) with normal indoor temperature is a likely indication of low airflow.
Some tools that measure airflow include TrueFlow grids, vane anemometers, and hot wire anemometers. However, these are advanced tools, and each one has its limitations. So, the best way to spot a system airflow problem is to perform those inspections with your senses and take your standard measurements.
As air moves over the evaporator coil, it comes into contact with the fins. Heat moves from the air to those fins, as heat moves from warm air to the colder fins. That heat transfer is critical for moving heat from a space, and fins help the evaporator maintain pressure.
When you have low airflow, the compressor amp draw will drop. The reduced pressure indicates that the refrigerant has less mass. The compressor does less work, but it doesn’t get cooled off as easily, and flooding is also possible.
In our class, we used the training equipment to simulate various low-airflow conditions. We also used the MeasureQuick app to profile the equipment, determine our ideal measurement ranges, and display our data. The MeasureQuick app determined that our superheat was hunting and that we were overfeeding our evaporator.
After troubleshooting the unit, we reduced our supply airflow. Our suction line pressure sharply decreased. We then jammed cardboard in the return duct, and our TESP sharply increased. Overall, our suction line temperature decreased sharply, TESP increased sharply, and subcooling increased slightly. MeasureQuick determined that we were running 249 CFM per ton, which indicates very low airflow.
Check out information on the 2022 HVACR Training Symposium at https://hvacrschool.com/symposium/.
Read all the tech tips, take the quizzes, and find our handy calculators at https://www.hvacrschool.com/.
Видео Impact of Airflow on Refrigerant Measurements and Performance канала HVAC School
Показать
Комментарии отсутствуют
Информация о видео
Другие видео канала
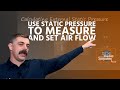
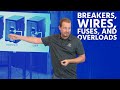
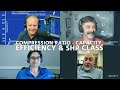

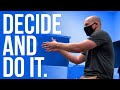
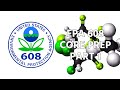

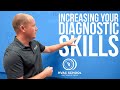
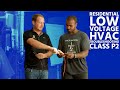
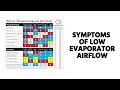
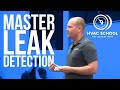
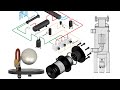
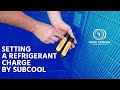
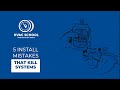
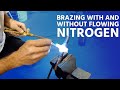

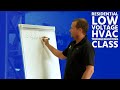
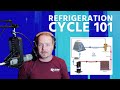

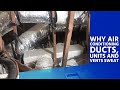