Making a spin casting mould, part 1: vulcanising
A rough run-through on how I make silicone moulds for model soldiers using low-temperature vulcanising silicone rubber. Part 2 will cover taking the mould out of the mould can and cutting feeds, kiss gates and vents.
The mould is vulcanised at 85 degrees C for 5 hours at 100 bar pressure (actually, I typically do 2.5 hours at 85C and then raise it to 90C for another 2.5 hours) This helps reduce shrinkage: vulcanising at higher temperatures requires less time but results in more shrinkage. It is possible to vulcanise the mould at 110C for just 1 hour, but shrinkage is high at about 5%. Vulcanising time also depends on the thickness of the mould discs.
The cream silicone discs are from J Coker of Faversham (http://j-coker.co.uk/). The discs have an IRHD of 70.
The 13mm square mould locator nuts are from Hewitt-Impex of Market Drayton (http://www.hewitt-impex.co.uk/). Hewitt's also supplies Nicem orange low-temperature vulcanising silicone discs, which have a pre-punched hole for the mould can mushroom.
Talc (French chalk) is available from several sources, including J Coker, and Tiranti (http://tiranti.co.uk/). Waitrose's unscented talc will also work.
I am not paid to endorse any of the companies or products mentioned: they are simply the suppliers and products that I regularly use in the UK.
Видео Making a spin casting mould, part 1: vulcanising канала Mr Saunders' Miniatures Workshop
The mould is vulcanised at 85 degrees C for 5 hours at 100 bar pressure (actually, I typically do 2.5 hours at 85C and then raise it to 90C for another 2.5 hours) This helps reduce shrinkage: vulcanising at higher temperatures requires less time but results in more shrinkage. It is possible to vulcanise the mould at 110C for just 1 hour, but shrinkage is high at about 5%. Vulcanising time also depends on the thickness of the mould discs.
The cream silicone discs are from J Coker of Faversham (http://j-coker.co.uk/). The discs have an IRHD of 70.
The 13mm square mould locator nuts are from Hewitt-Impex of Market Drayton (http://www.hewitt-impex.co.uk/). Hewitt's also supplies Nicem orange low-temperature vulcanising silicone discs, which have a pre-punched hole for the mould can mushroom.
Talc (French chalk) is available from several sources, including J Coker, and Tiranti (http://tiranti.co.uk/). Waitrose's unscented talc will also work.
I am not paid to endorse any of the companies or products mentioned: they are simply the suppliers and products that I regularly use in the UK.
Видео Making a spin casting mould, part 1: vulcanising канала Mr Saunders' Miniatures Workshop
Показать
Комментарии отсутствуют
Информация о видео
20 декабря 2019 г. 18:19:26
00:17:34
Другие видео канала
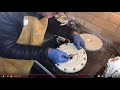
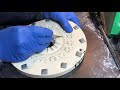
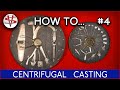
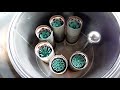
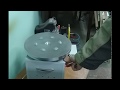
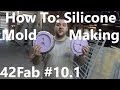

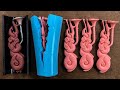



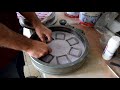


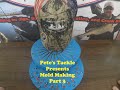

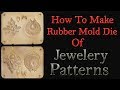
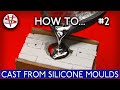
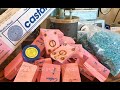
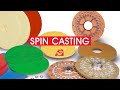