Maintenance for Your Screen Printing Press | Matsui Water Based Screen Printing Class
Whether you run a Sportsman, a Diamondback, a Gauntlet, a Challenger or any of M&R’s other automatic screen printing presses, you need to do routine maintenance. “Schedule your maintenance, or your machine will schedule it for you – and it doesn’t care about your deadlines.”
Visit M&R online: https://www.mrprint.com
For about $30, you can procure all you need to maintain your screen printing press. M&R machines use 10 weight non-detergent oil to lubricate all of their pneumatic pumps. You also need regular grease, ideally super synthetic grease with teflon coverage. You can use that grease on just about every machine in your print shop EXCEPT for your curing dryer! For your dryer, you will need high temperature grease. Definitely don’t mix the two types of grease!
Rules for screen printing press maintenance:
Keep your machine clean. Spray tack is notorious for making sticky surfaces where lint, dirt, ink, and all kinds of debris can accumulate. Cut down on spray tack usage (if possible), but set aside time every day to wipe down and clean your machine. This doesn’t need to be a deep cleaning – a simple once-over every day will save you lots of time in the long run.
Check for water in the main regulator filter every day. You never know if your compressor or chiller is working properly. If water gets into your pneumatic parts, it’s like poison for the o-ring seals in your machine. This is a super simple daily task that will prevent a LOT of issues.
Don’t turn off your compressor and chiller every day. Chillers take 6 to 8 hours to get to maximum efficiency. If you turn your chiller on in the morning, it’s not doing its job until the end of the working day. Leave it on during the work week. If your lines are leaking air during the night, you should address the leakage issues with your press. There is simply no need to turn off your compressor and chiller every evening!
Read the manual for your machine. M&R machines have a in-depth page in EVERY manual that has a specific calendar for maintenance. It offers a daily task list you can follow.
Clean your registration bearings every two weeks. For ten to fifteen minutes every two weeks, you can keep your machine in good working order and ensure fast registration over the long term.
This video will show you how to check for water in your screen printing press' pneumatic lines, how to check the oiler to assure that oil is actually lubricating your machine, how to maintain your registration bearings, where to apply grease to your print heads and center shaft, and more!
Regular maintenance is a key to success. Downtime is inevitable, but you can eliminate your press as a source for downtime with a persistent eye toward cleanliness and meticulously following your machine manufacturer’s suggested maintenance routine.
Try Printavo: https://www.printavo.com
Check out Printavo Merch: https://www.printavo.com/merch
Follow us on Instagram for all of the latest updates: https://www.instagram.com/printavo
Subscribe to our channel! New videos every day!
Видео Maintenance for Your Screen Printing Press | Matsui Water Based Screen Printing Class канала Printavo
Visit M&R online: https://www.mrprint.com
For about $30, you can procure all you need to maintain your screen printing press. M&R machines use 10 weight non-detergent oil to lubricate all of their pneumatic pumps. You also need regular grease, ideally super synthetic grease with teflon coverage. You can use that grease on just about every machine in your print shop EXCEPT for your curing dryer! For your dryer, you will need high temperature grease. Definitely don’t mix the two types of grease!
Rules for screen printing press maintenance:
Keep your machine clean. Spray tack is notorious for making sticky surfaces where lint, dirt, ink, and all kinds of debris can accumulate. Cut down on spray tack usage (if possible), but set aside time every day to wipe down and clean your machine. This doesn’t need to be a deep cleaning – a simple once-over every day will save you lots of time in the long run.
Check for water in the main regulator filter every day. You never know if your compressor or chiller is working properly. If water gets into your pneumatic parts, it’s like poison for the o-ring seals in your machine. This is a super simple daily task that will prevent a LOT of issues.
Don’t turn off your compressor and chiller every day. Chillers take 6 to 8 hours to get to maximum efficiency. If you turn your chiller on in the morning, it’s not doing its job until the end of the working day. Leave it on during the work week. If your lines are leaking air during the night, you should address the leakage issues with your press. There is simply no need to turn off your compressor and chiller every evening!
Read the manual for your machine. M&R machines have a in-depth page in EVERY manual that has a specific calendar for maintenance. It offers a daily task list you can follow.
Clean your registration bearings every two weeks. For ten to fifteen minutes every two weeks, you can keep your machine in good working order and ensure fast registration over the long term.
This video will show you how to check for water in your screen printing press' pneumatic lines, how to check the oiler to assure that oil is actually lubricating your machine, how to maintain your registration bearings, where to apply grease to your print heads and center shaft, and more!
Regular maintenance is a key to success. Downtime is inevitable, but you can eliminate your press as a source for downtime with a persistent eye toward cleanliness and meticulously following your machine manufacturer’s suggested maintenance routine.
Try Printavo: https://www.printavo.com
Check out Printavo Merch: https://www.printavo.com/merch
Follow us on Instagram for all of the latest updates: https://www.instagram.com/printavo
Subscribe to our channel! New videos every day!
Видео Maintenance for Your Screen Printing Press | Matsui Water Based Screen Printing Class канала Printavo
Показать
Комментарии отсутствуют
Информация о видео
Другие видео канала
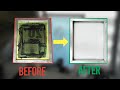
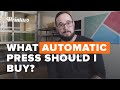
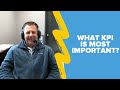

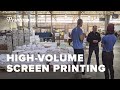
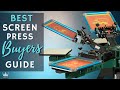
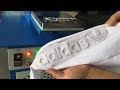
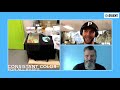
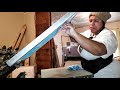
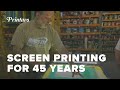



![How To Press A Multi Color Heat Transfer Vinyl (HTV) Design [3 Color T-Shirt Design Using 2 Colors]](https://i.ytimg.com/vi/k3Sx7VuaWTY/default.jpg)



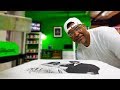

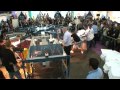