HOW PRECAST CONCRETE ROOF SLABS ARE MADE|FACTORY TOUR|STEPS STAIRS BALCONIES CEILING FORMWORK
IF MY VIDEO HELPED YOU, FEEL FREE TO DONATE TO SUPPORT MY WORK! THANK YOU! PAYPALme: http://bit.ly/supportCarl
Hi this is Carl the landscape guy. Not only are precast concrete parts used in landscaping, but all the more so in building construction. I had the opportunity to see the production of prefabricated elements at the company FDU Germany. Here in the factory, stairs, balconies and ceilings are being manufactured as concrete components. For the stairs, they first create an appropriate formwork. The formwork can be reused several times. For spiral staircases, these large boxes are used for the formwork. According to plan the steps are then mounted as negative production on the wall. The entire stairway section is concreted upside down. But before that, the reinforcing irons are brought in accordingly. From the bottom, the stairs are smoothed immediately after concreting. The reinforcement connecting irons are very important. They make it possible for the stairs to be concreted on the ceiling or wall on the construction site and permanently connected properly. Mounting loops can also be embedded in the components so that loading and transport to the installation site with a crane is easier. The stairs are stored outside for curing. The concrete takes 28 days to reach its full strength. By means of various formwork inserts, the stairs can be concreted with the non-slip surfaces desired by the customer. Or, as here, edge strips can be cast in as well. Also balcony bottoms are manufactured here. The reinforcement irons are very important here, as well. The reinforcements are precisely sized by engineers and then prefabricated according to plan and placed in the formwork. Here you can see again the connecting reinforcement irons, which preserve the balcony later from breaking off the house. Here, too, threads are embedded in the concrete in order to simplify transportation. The FDU company specializes in the production of ready-made ceilings. For these, oversized steel tables are used. A robot cleans the table and distributes the spacers, which set the ceiling size later. Then the table rolls to the reinforcement department. Here, the reinforcing steel is automatically cut to length by robots according to the static plan and spread on the table. Manually, the process is checked and rectified, if necessary. Parts of the iron will stick out of the top surface of the ceiling. The production table then continues to concreting. At FDU, they mix their concrete directly on site. It is important that the right concrete quality and strength is maintained. The computer controlled machine moves across the table and drops the right amount of concrete. The subsequent shaking distributes the concrete, so that the ceiling has the same thickness everywhere. In addition, air bubbles or inclusions escape, so that the concrete later does not become porous and the iron is well enclosed. The worker attaches a sticker containing the construction site and date of manufacture, so that the part can later be assigned accurately. These hanging irons are dropped on the onward journey so that the surface is roughened. This ensures a better bond to the on-site concrete layer later. The table continues and is stored for about 1 day to cure in a heated storage. Then the finished ceilings can be removed from the table. The crane grabs the ceiling by the reinforcement irons and stacks it for transport. The ceilings also have to harden for some time before they can be transported and installed. Meanwhile, the table is already running the next round in the production line. Arriving at the construction site of my house, the ceilings can be laid on the walls and temporary supports. All necessary cables and wires and additional reinforcement mats are simply laid on the pre-built ceiling. Then the final concrete layer can be applied with only some formwork on the side. After flattening the top surface the ceiling is done. I hope you enjoyed this video about precast concrete production. It was a great opportunity to be at FDU’s production site. Their well organized and efficient process left a good impression on me. Many thanks to FDU Germany for the recording permission and guidance. On my channel you will find many more construction videos, so don't forget to subscribe. Smash that like button and feel free to leave a comment. See you next time, I’m Carl the landscape guy.
Видео HOW PRECAST CONCRETE ROOF SLABS ARE MADE|FACTORY TOUR|STEPS STAIRS BALCONIES CEILING FORMWORK канала CarlTheLandscapeGuy
Hi this is Carl the landscape guy. Not only are precast concrete parts used in landscaping, but all the more so in building construction. I had the opportunity to see the production of prefabricated elements at the company FDU Germany. Here in the factory, stairs, balconies and ceilings are being manufactured as concrete components. For the stairs, they first create an appropriate formwork. The formwork can be reused several times. For spiral staircases, these large boxes are used for the formwork. According to plan the steps are then mounted as negative production on the wall. The entire stairway section is concreted upside down. But before that, the reinforcing irons are brought in accordingly. From the bottom, the stairs are smoothed immediately after concreting. The reinforcement connecting irons are very important. They make it possible for the stairs to be concreted on the ceiling or wall on the construction site and permanently connected properly. Mounting loops can also be embedded in the components so that loading and transport to the installation site with a crane is easier. The stairs are stored outside for curing. The concrete takes 28 days to reach its full strength. By means of various formwork inserts, the stairs can be concreted with the non-slip surfaces desired by the customer. Or, as here, edge strips can be cast in as well. Also balcony bottoms are manufactured here. The reinforcement irons are very important here, as well. The reinforcements are precisely sized by engineers and then prefabricated according to plan and placed in the formwork. Here you can see again the connecting reinforcement irons, which preserve the balcony later from breaking off the house. Here, too, threads are embedded in the concrete in order to simplify transportation. The FDU company specializes in the production of ready-made ceilings. For these, oversized steel tables are used. A robot cleans the table and distributes the spacers, which set the ceiling size later. Then the table rolls to the reinforcement department. Here, the reinforcing steel is automatically cut to length by robots according to the static plan and spread on the table. Manually, the process is checked and rectified, if necessary. Parts of the iron will stick out of the top surface of the ceiling. The production table then continues to concreting. At FDU, they mix their concrete directly on site. It is important that the right concrete quality and strength is maintained. The computer controlled machine moves across the table and drops the right amount of concrete. The subsequent shaking distributes the concrete, so that the ceiling has the same thickness everywhere. In addition, air bubbles or inclusions escape, so that the concrete later does not become porous and the iron is well enclosed. The worker attaches a sticker containing the construction site and date of manufacture, so that the part can later be assigned accurately. These hanging irons are dropped on the onward journey so that the surface is roughened. This ensures a better bond to the on-site concrete layer later. The table continues and is stored for about 1 day to cure in a heated storage. Then the finished ceilings can be removed from the table. The crane grabs the ceiling by the reinforcement irons and stacks it for transport. The ceilings also have to harden for some time before they can be transported and installed. Meanwhile, the table is already running the next round in the production line. Arriving at the construction site of my house, the ceilings can be laid on the walls and temporary supports. All necessary cables and wires and additional reinforcement mats are simply laid on the pre-built ceiling. Then the final concrete layer can be applied with only some formwork on the side. After flattening the top surface the ceiling is done. I hope you enjoyed this video about precast concrete production. It was a great opportunity to be at FDU’s production site. Their well organized and efficient process left a good impression on me. Many thanks to FDU Germany for the recording permission and guidance. On my channel you will find many more construction videos, so don't forget to subscribe. Smash that like button and feel free to leave a comment. See you next time, I’m Carl the landscape guy.
Видео HOW PRECAST CONCRETE ROOF SLABS ARE MADE|FACTORY TOUR|STEPS STAIRS BALCONIES CEILING FORMWORK канала CarlTheLandscapeGuy
Показать
Комментарии отсутствуют
Информация о видео
Другие видео канала
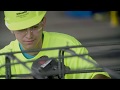
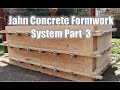

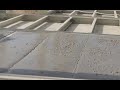
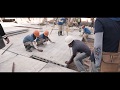
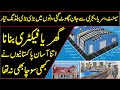

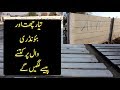

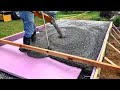
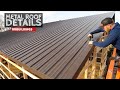
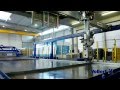

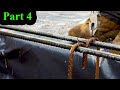

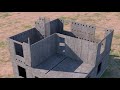
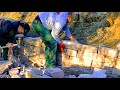
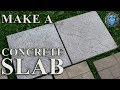

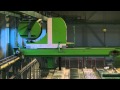