Bead Blasting Tips for Long Bead Life and Best Finish
I want to give you some tips on how to improve your bead blasting. I'd say about 90% of the bead blasting jobs I've seen, was where the finish was mostly a matte finish with a little satin finish to it, but still pretty poor. I've seen this so often that I figured it would be a good idea to do a video on this to show one way of getting good results with your bead blaster. Glass beads have been really popular for many years. Unfortunately, many people see them as a silver bullet for restoration. They expect the beads to clean the parts and leave a great finish, and also clean off all the rust and scale and oxidation from any part. But it's a compromise like everything else. So, here are some tips on how to get the best finished you can with glass beads.
1. Turn your pressure down. Glass beads are meant to be used at lower pressures, so turn down your pressure as low as possible. This is the most important factor for increasing the life of your beads and yielding a higher finish. Remember, this stuff is glass, and we all know what happens to glass when throw it at a hard object. I use about 50 psi with my siphon blaster. Glass beads are finishing media. They are smooth and round and not designed to cut. They are made to burnish a surface, just like round tumbling media does, but at a higher rate. Keep in mind that the pressure used create a high finish will not clean a surface. It won't even remove water stains. If you turn the pressure up to try to get around that, the beads will start to clean, but they also begin to smash on impact with your part, essentially turning the beads into crushed glass. Crushed glass is a very effective blasting media, by the way. However, there is no sense in buying expensive high quality glass beads, like Potter's or Ballotini, just to smash them into dust to clean your parts. If you're going to do that, buy crushed glass instead and run at a moderate pressure. It's a lot cheaper than beads. Also, when you smash beads into your parts, you start producing excess dust and sharp particles which falls onto the rest of the clean beads and contaminates them, which in turn gets picked up with the good beads and degrades the finish. It almost goes without saying that when higher pressures smash the beads on impact, that many of those particles are going to get embedded in the surface. If the part you are blasting is an internal engine part that is exposed to a heating and cooling cycle or oil, you know this is a very bad idea.
2. You can't put a great finish on aluminum without stripping off the oxide layer, which glass beads are not designed to do. Instead, use a dedicated sharp cutting abrasive to clean off the oxide or rust, such as crushed glass, black beauty, aluminum oxide, etc. My preferred abrasive by far is crushed glass, because it cleans as fast as aluminum oxide and silicon carbide, but is very clean, and a fraction of the cost. It also doesn't stick to all your parts and the cabinet window like aluminum oxide and won't shock you every few seconds. Use a fine abrasive, about 60 mesh or finer, or anything with a flour like consistency. It will quickly remove the grey oxide from aluminum and rust from steel. The down side of using a dedicated abrasive is you now need another blaster. But what if you can't or don't want to get another cabinet. In that case, I recommend just getting a portable blaster. There are several types. The least expensive is the siphon blaster with a pick up tube. There are also blasters that have the abrasive hopper built into he blaster itself. I've used both. The most expensive portable blaster would be the pressuring tank units. In that case, you might as well just buy another cabinet if you have the room. You can also switch out media using your current cabinet, though that gets old quickly. If you're using a portable blaster, make sure you wear an N99 respirator, face shield, and gloves. Respirators are cheap insurance for your lungs, and can be ordered through Mcmaster carr or msc.
3. When bead blasting, make sure your air is dry and oil free, not only to prevent clogs, but to prevent moisture tarnishing the surface. Older Japanese castings are especially prone to this because of higher copper content. A few seconds of moist air hitting one of these freshly exposed aluminum surface will begin to discolor it. Further bead blasting will only make it worse.
4. All glass beads leave a satin finish, but generally speaking, the lower the mesh size, the brighter the finish.
Видео Bead Blasting Tips for Long Bead Life and Best Finish канала Arnold's Design
1. Turn your pressure down. Glass beads are meant to be used at lower pressures, so turn down your pressure as low as possible. This is the most important factor for increasing the life of your beads and yielding a higher finish. Remember, this stuff is glass, and we all know what happens to glass when throw it at a hard object. I use about 50 psi with my siphon blaster. Glass beads are finishing media. They are smooth and round and not designed to cut. They are made to burnish a surface, just like round tumbling media does, but at a higher rate. Keep in mind that the pressure used create a high finish will not clean a surface. It won't even remove water stains. If you turn the pressure up to try to get around that, the beads will start to clean, but they also begin to smash on impact with your part, essentially turning the beads into crushed glass. Crushed glass is a very effective blasting media, by the way. However, there is no sense in buying expensive high quality glass beads, like Potter's or Ballotini, just to smash them into dust to clean your parts. If you're going to do that, buy crushed glass instead and run at a moderate pressure. It's a lot cheaper than beads. Also, when you smash beads into your parts, you start producing excess dust and sharp particles which falls onto the rest of the clean beads and contaminates them, which in turn gets picked up with the good beads and degrades the finish. It almost goes without saying that when higher pressures smash the beads on impact, that many of those particles are going to get embedded in the surface. If the part you are blasting is an internal engine part that is exposed to a heating and cooling cycle or oil, you know this is a very bad idea.
2. You can't put a great finish on aluminum without stripping off the oxide layer, which glass beads are not designed to do. Instead, use a dedicated sharp cutting abrasive to clean off the oxide or rust, such as crushed glass, black beauty, aluminum oxide, etc. My preferred abrasive by far is crushed glass, because it cleans as fast as aluminum oxide and silicon carbide, but is very clean, and a fraction of the cost. It also doesn't stick to all your parts and the cabinet window like aluminum oxide and won't shock you every few seconds. Use a fine abrasive, about 60 mesh or finer, or anything with a flour like consistency. It will quickly remove the grey oxide from aluminum and rust from steel. The down side of using a dedicated abrasive is you now need another blaster. But what if you can't or don't want to get another cabinet. In that case, I recommend just getting a portable blaster. There are several types. The least expensive is the siphon blaster with a pick up tube. There are also blasters that have the abrasive hopper built into he blaster itself. I've used both. The most expensive portable blaster would be the pressuring tank units. In that case, you might as well just buy another cabinet if you have the room. You can also switch out media using your current cabinet, though that gets old quickly. If you're using a portable blaster, make sure you wear an N99 respirator, face shield, and gloves. Respirators are cheap insurance for your lungs, and can be ordered through Mcmaster carr or msc.
3. When bead blasting, make sure your air is dry and oil free, not only to prevent clogs, but to prevent moisture tarnishing the surface. Older Japanese castings are especially prone to this because of higher copper content. A few seconds of moist air hitting one of these freshly exposed aluminum surface will begin to discolor it. Further bead blasting will only make it worse.
4. All glass beads leave a satin finish, but generally speaking, the lower the mesh size, the brighter the finish.
Видео Bead Blasting Tips for Long Bead Life and Best Finish канала Arnold's Design
Показать
Комментарии отсутствуют
Информация о видео
Другие видео канала
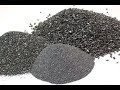




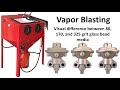

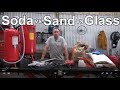
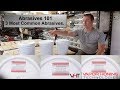
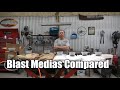
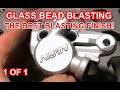
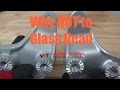

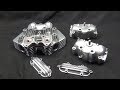
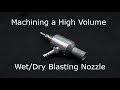
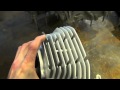
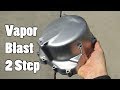

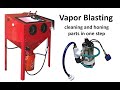
