Team Macy's - GT Capstone Spring 2016
Macy's Carton Estimation team focused on small ticket items and direct to consumer items from Macys.com online business. The problem was that the Macy's distribution center (DC) was either under-scheduling or overscheduling workers due to scheduled freight not arriving on-time (either too early or too late). The GT team found that some distribution centers were experiencing around 50% of their scheduled freight not arriving on-time. Macy's freight processing policy was First-In-First-Out (FIFO). If freight arrived 2 days early, the DC would be under-scheduled for a period of time, followed immediately by being overscheduled.
The team implemented a "First Scheduled, First Out Policy" at the DC. With this logic, freight arriving more than 2 days early would be rescheduled, while freight arriving on-time would be processed first. This model would save Macy's over $100K annually in overscheduled labor.
Additionally, the GT team created a Performance Analysis Tool (PAT) that provided a dashboard interface to analyze freight arrivals and help identify causes of arrival time variability by carrier.
Видео Team Macy's - GT Capstone Spring 2016 канала Caroline Dunn
The team implemented a "First Scheduled, First Out Policy" at the DC. With this logic, freight arriving more than 2 days early would be rescheduled, while freight arriving on-time would be processed first. This model would save Macy's over $100K annually in overscheduled labor.
Additionally, the GT team created a Performance Analysis Tool (PAT) that provided a dashboard interface to analyze freight arrivals and help identify causes of arrival time variability by carrier.
Видео Team Macy's - GT Capstone Spring 2016 канала Caroline Dunn
Показать
Комментарии отсутствуют
Информация о видео
Другие видео канала
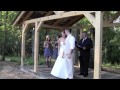

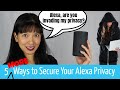
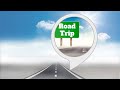
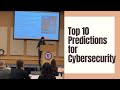
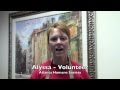
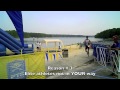
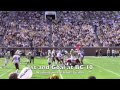
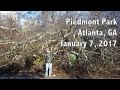
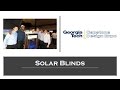
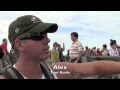
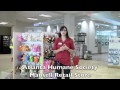

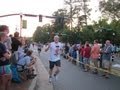
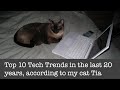
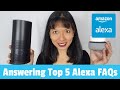
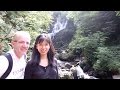

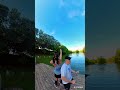
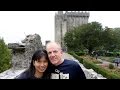