Ball Mill Critical Speed & Working Principle
https://www.911metallurgist.com/blog/ball-mill Learn about Ball Mill Critical Speed and its effect on inner charge movements. The effect of Ball Mill RPM speed going from sub-critical to super-critical helps understand the Ball Mill Working Principles of ball-on-ball VS ball-on-shell grinding.
The Motion of the Ball Charge
The input energy in ball milling is that applied by the drive to impart motion to the mill charge. Since the usefull output is that which goes into breakage of the feed material, it is apparent that it is the point at which the energy of motion of the media is dissipated that is of concern.
Single Particle Motion: The outer row of balls being acted upon directly by the mill shell is prominent it, determining the motion of the entire charge. Besides dissipating a significant fraction of the total energy consumed by the mill (for example, the outer row of 50 mm diameter balls in a 4 meter diameter mill consumes close to one tenth of the total power delivered by the drive in being lifted and dropped), the outer row is the only portion of the charge in direct contact with the shell, and so forms the key link for energy transmission to the remainder of the charge.
The only assumptions required for determination of the single ball trajectory are a coefficient of friction between the ball and mill lining, and unobstructed free fall after movement away from the lining commences.
Although recognizably somewhat idealized, two interesting assertions were noted as a result of the analysis, as follows:
a) Particle trajectory is independent of mill diameter. Although simply a confirmation of the basis for use of percent of critical, the most common form for describing mill rotational speed, the implication is more far-reaching. If 75 percent of critical speed is considered desirable for efficient grinding in a 2.4 meter (8 foot) diameter mill, then the same will be true for a 5.0 meter (15½ foot) diameter mill. At least in terms of effective charge motion, then, there is no justification for resorting to lower mill critical speeds at larger mill diameters.
b) Particle trajectory is highly sensitive to liner lifter face angle. As can be seen in Figures 1 and 2, a change of lifter angle from zero (vertical) to thirty degrees results in a greatly subdued trajectory.
The implications for machine performance are first; that power draw will vary with different original liner designs, as well as throughout the wear life, depending on the wear pattern; and secondly, that a desireable trajectory, even if achieved by the original liner design, will not be maintained unless the wear pattern is such that a consistent overall mill lining profile is maintained.
Complete Charge Motion: Extension of ball charge motion studies to include the entire charge encompasses numerous complexities beyond both the scope of this paper and the extent of present investigations. However, a few observations considered relevant to this discussion are listed below:
a) Ball charge level has a significant effect on overall charge motion. The tendency of the charge to slip back along the rising side of the shell is reduced as charge level increases, until reaching between 30 to 40 percent of mill volume (in one particular test mill) where slip ceases. Increased charge level (given fixed critical speed) beyond this level results in more cataracting (flying) as opposed to cascading (rolling) action of the balls, but only to the extent of about 50 percent of mill volume where swelling and crowding obliterates cataracting action by leaving no space for free falling.
b) A definite transverse segregation of ball sizes is visible in the cross-section of a normally graded charge, with the large balls found at the perimeter at low speeds, and at the charge centre for high speeds. The reverse is of course true for the small balls, and more importantly, for coarse ore particles, which are more closely associated with the small balls in their dimensions.
c) Increased lifter height, or reduced ball diameter, results in higher trajectories of the outer row of balls. However, within the range of normal (North American) operating practice (i.e. 35 - 40% mill loading, and 70 - 80% of critical speed) and for ball-size approximating the lifter height, the trajectories of the outer row are relatively unaffected by subsequent rows. This may be expected due to the lack of direct support from a lifter and the lower percentage of critical speed at reduced diameter.
Видео Ball Mill Critical Speed & Working Principle канала 911 Metallurgy Corp.
The Motion of the Ball Charge
The input energy in ball milling is that applied by the drive to impart motion to the mill charge. Since the usefull output is that which goes into breakage of the feed material, it is apparent that it is the point at which the energy of motion of the media is dissipated that is of concern.
Single Particle Motion: The outer row of balls being acted upon directly by the mill shell is prominent it, determining the motion of the entire charge. Besides dissipating a significant fraction of the total energy consumed by the mill (for example, the outer row of 50 mm diameter balls in a 4 meter diameter mill consumes close to one tenth of the total power delivered by the drive in being lifted and dropped), the outer row is the only portion of the charge in direct contact with the shell, and so forms the key link for energy transmission to the remainder of the charge.
The only assumptions required for determination of the single ball trajectory are a coefficient of friction between the ball and mill lining, and unobstructed free fall after movement away from the lining commences.
Although recognizably somewhat idealized, two interesting assertions were noted as a result of the analysis, as follows:
a) Particle trajectory is independent of mill diameter. Although simply a confirmation of the basis for use of percent of critical, the most common form for describing mill rotational speed, the implication is more far-reaching. If 75 percent of critical speed is considered desirable for efficient grinding in a 2.4 meter (8 foot) diameter mill, then the same will be true for a 5.0 meter (15½ foot) diameter mill. At least in terms of effective charge motion, then, there is no justification for resorting to lower mill critical speeds at larger mill diameters.
b) Particle trajectory is highly sensitive to liner lifter face angle. As can be seen in Figures 1 and 2, a change of lifter angle from zero (vertical) to thirty degrees results in a greatly subdued trajectory.
The implications for machine performance are first; that power draw will vary with different original liner designs, as well as throughout the wear life, depending on the wear pattern; and secondly, that a desireable trajectory, even if achieved by the original liner design, will not be maintained unless the wear pattern is such that a consistent overall mill lining profile is maintained.
Complete Charge Motion: Extension of ball charge motion studies to include the entire charge encompasses numerous complexities beyond both the scope of this paper and the extent of present investigations. However, a few observations considered relevant to this discussion are listed below:
a) Ball charge level has a significant effect on overall charge motion. The tendency of the charge to slip back along the rising side of the shell is reduced as charge level increases, until reaching between 30 to 40 percent of mill volume (in one particular test mill) where slip ceases. Increased charge level (given fixed critical speed) beyond this level results in more cataracting (flying) as opposed to cascading (rolling) action of the balls, but only to the extent of about 50 percent of mill volume where swelling and crowding obliterates cataracting action by leaving no space for free falling.
b) A definite transverse segregation of ball sizes is visible in the cross-section of a normally graded charge, with the large balls found at the perimeter at low speeds, and at the charge centre for high speeds. The reverse is of course true for the small balls, and more importantly, for coarse ore particles, which are more closely associated with the small balls in their dimensions.
c) Increased lifter height, or reduced ball diameter, results in higher trajectories of the outer row of balls. However, within the range of normal (North American) operating practice (i.e. 35 - 40% mill loading, and 70 - 80% of critical speed) and for ball-size approximating the lifter height, the trajectories of the outer row are relatively unaffected by subsequent rows. This may be expected due to the lack of direct support from a lifter and the lower percentage of critical speed at reduced diameter.
Видео Ball Mill Critical Speed & Working Principle канала 911 Metallurgy Corp.
Показать
Комментарии отсутствуют
Информация о видео
Другие видео канала
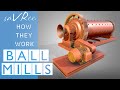
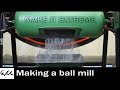
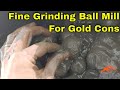


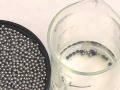

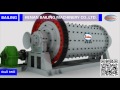
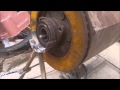
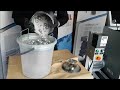

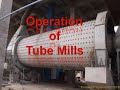
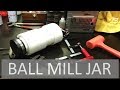
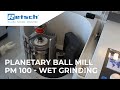
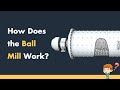
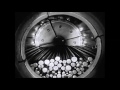

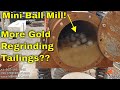
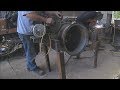
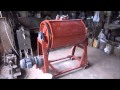