MINI Countryman Electric and Petrol Engine - PRODUCTION
Production launch of the MINI Countryman Electric at BMW Group Plant Leipzig
00:00 - Intro
00:27 - MINI Countryman Electric Pre-Assembly
03:35 - MINI Countryman Electric Assembly
08:49 - High Voltage Battery Assembly
13:17 - Final Check Assembly
14:29 - MINI Countryman Press Shop
15:43 - MINI Countryman Body Shop
19:12 - Conveyor Belts In The Central Building
20:36 - MINI Countryman Paint Shop
27:57 - Exterior Plastic Components
30:15 - MINI Countryman Assembly Line
37:34 - MINI Countryman Finish Line
#mini #carfactory #production #minicountryman #assembly #electricvehicles
Electrification continues at BMW Group Plant Leipzig: Four months after launching production of the combustion-engined MINI Countryman, the all-electric version is now rolling off the lines at Leipzig as well. After phasing out production of the BMW i3, the birthplace of electric mobility at the BMW Group has welcomed another fully electric car to its range. It now manufactures four models with three drive types by two brands, all on a single production line: the BMW 1 Series, the BMW 2 Series Active Tourer (including the plug-in hybrid version), the BMW 2 Series Gran Coupe and the MINI Countryman in both its fully electric and combustion-powered versions.
The MINI Countryman Electric represents a major step in the MINI brand’s transition to full electrification by 2030 and combines an electrified go-kart feel with zero local emissions mobility. It comes in two fully electric variants: the Countryman E (150 kW, 204 hp | electricity consumption 17.4 – 15.7 kWh/100 km | CO2 emissions 0 g/km) and the more powerful all-wheel Countryman SE ALL4 (230 kW, 313 hp | electricity consumption 18.5 – 16.8 kWh/100 km | CO2 emissions 0 g/km).
Consistent plant upgrades and flexible production system
To enable production of up to 350,000 units a year – 100,000 more than previously – Plant Leipzig has been continuously upgraded since 2018, with extensive additions and upgrades to the bodyshop, paintshop, assembly and logistics. “Our cars and components are very much in demand. In recent years the BMW Group has invested around 1.6 billion euros in the Leipzig site to produce additional vehicles and electric components, and now we’re increasing vehicle volumes too – which is great news for our plant,” said Petra Peterhänsel, Plant Director.
The main driver behind the volume increase is the MINI Countryman. During the course of 2024, output will rise to almost 500 units a day – on top of the 800 or so BMW vehicles the plant is producing. What’s more, thanks to its flexible production system, Plant Leipzig is in a position to respond quickly to customer demand, for example by increasing the share of fully electric vehicles.
Flexible assembly structures also meant the MINI Countryman Electric could be integrated seamlessly into production. The situation is similar with the different drive units, which are all produced on one and the same line in aggregate assembly and prepared for what’s known as “marriage” with the body. The e-drives, transmissions and control electronics (collectively known as the highly integrated electric drive topology, or HEAT) for the two all-electric models are connected directly in the plant. A new production line was required only for the control electronics.
⚡️ Discover ALL new cars before anyone else! SUBSCRIBE Now to Gommeblog Car and Performance ► http://goo.gl/sP8oKK
🔔 Don’t miss next videos: Press the little bell ((🔔)) to get notifications
🖥 My website ► https://www.gommeblog.it/
🔥 JOIN: Memberships Link ► https://www.youtube.com/channel/UCl5ijI4ZXN2ki7PeQajbFrA/join
Видео MINI Countryman Electric and Petrol Engine - PRODUCTION канала GommeBlog.it: Tecnica e Performance
00:00 - Intro
00:27 - MINI Countryman Electric Pre-Assembly
03:35 - MINI Countryman Electric Assembly
08:49 - High Voltage Battery Assembly
13:17 - Final Check Assembly
14:29 - MINI Countryman Press Shop
15:43 - MINI Countryman Body Shop
19:12 - Conveyor Belts In The Central Building
20:36 - MINI Countryman Paint Shop
27:57 - Exterior Plastic Components
30:15 - MINI Countryman Assembly Line
37:34 - MINI Countryman Finish Line
#mini #carfactory #production #minicountryman #assembly #electricvehicles
Electrification continues at BMW Group Plant Leipzig: Four months after launching production of the combustion-engined MINI Countryman, the all-electric version is now rolling off the lines at Leipzig as well. After phasing out production of the BMW i3, the birthplace of electric mobility at the BMW Group has welcomed another fully electric car to its range. It now manufactures four models with three drive types by two brands, all on a single production line: the BMW 1 Series, the BMW 2 Series Active Tourer (including the plug-in hybrid version), the BMW 2 Series Gran Coupe and the MINI Countryman in both its fully electric and combustion-powered versions.
The MINI Countryman Electric represents a major step in the MINI brand’s transition to full electrification by 2030 and combines an electrified go-kart feel with zero local emissions mobility. It comes in two fully electric variants: the Countryman E (150 kW, 204 hp | electricity consumption 17.4 – 15.7 kWh/100 km | CO2 emissions 0 g/km) and the more powerful all-wheel Countryman SE ALL4 (230 kW, 313 hp | electricity consumption 18.5 – 16.8 kWh/100 km | CO2 emissions 0 g/km).
Consistent plant upgrades and flexible production system
To enable production of up to 350,000 units a year – 100,000 more than previously – Plant Leipzig has been continuously upgraded since 2018, with extensive additions and upgrades to the bodyshop, paintshop, assembly and logistics. “Our cars and components are very much in demand. In recent years the BMW Group has invested around 1.6 billion euros in the Leipzig site to produce additional vehicles and electric components, and now we’re increasing vehicle volumes too – which is great news for our plant,” said Petra Peterhänsel, Plant Director.
The main driver behind the volume increase is the MINI Countryman. During the course of 2024, output will rise to almost 500 units a day – on top of the 800 or so BMW vehicles the plant is producing. What’s more, thanks to its flexible production system, Plant Leipzig is in a position to respond quickly to customer demand, for example by increasing the share of fully electric vehicles.
Flexible assembly structures also meant the MINI Countryman Electric could be integrated seamlessly into production. The situation is similar with the different drive units, which are all produced on one and the same line in aggregate assembly and prepared for what’s known as “marriage” with the body. The e-drives, transmissions and control electronics (collectively known as the highly integrated electric drive topology, or HEAT) for the two all-electric models are connected directly in the plant. A new production line was required only for the control electronics.
⚡️ Discover ALL new cars before anyone else! SUBSCRIBE Now to Gommeblog Car and Performance ► http://goo.gl/sP8oKK
🔔 Don’t miss next videos: Press the little bell ((🔔)) to get notifications
🖥 My website ► https://www.gommeblog.it/
🔥 JOIN: Memberships Link ► https://www.youtube.com/channel/UCl5ijI4ZXN2ki7PeQajbFrA/join
Видео MINI Countryman Electric and Petrol Engine - PRODUCTION канала GommeBlog.it: Tecnica e Performance
Показать
Комментарии отсутствуют
Информация о видео
3 марта 2024 г. 15:35:35
00:39:16
Другие видео канала
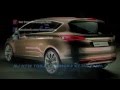
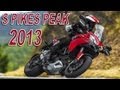
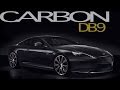
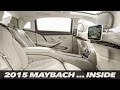

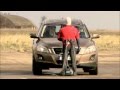
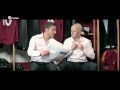
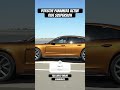

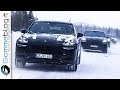
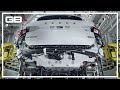
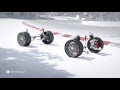
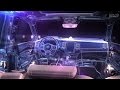
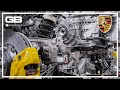
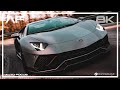
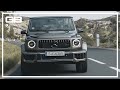
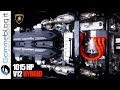
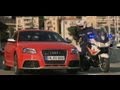

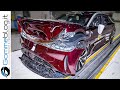
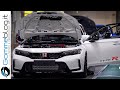