Optimizing the Reaction Furnace
This video is the first in the SRU Optimization series, which describes how to optimize the performance of each individual process unit, and covers 2 case studies from past testing experiences at SRE.
The reaction furnace is the vessel where the thermal combustion reaction takes place. This is a Free-flame reaction inside a refractory lined vessel (corrosion related).
• This is also where the majority of the overall conversion of H2S to sulfur occurs (50 to 75%).
• There are many side reactions in the reaction furnace, creating unwanted products like CO, H2, COS and CS2
• For sufficient flame stability, a minimum temperature of 900 C (1650 F) is needed, however
• Temperatures above 1050 C are desired for the adequate destruction of contaminants like BTEX, mercaptans, NH3, HCN, methanol, HCs
• The reaction furnace is kinetically limited based on residence time, turbulence, and temperature, as well as burner efficiency.
The SRU is only as good as what it receives for feed streams. RF temperature is typically directly proportional to H2S content, this further illustrates the importance of the amine and SWS units. SRE can test these upstream units as well, optimizing for higher H2S contents and CO2 slip, and minimized hydrocarbon pickup.
In refineries, the sour water stripper sends a mixture of typically 1/3 H2S, 1/3, water, and 1/3 ammonia (NH3) to the SRU. If the ammonia is not fully destroyed in the reaction furnace, residuals can carry over to the condensers and converters, risking the formation of ammonia salts. These salts negatively impact heat transfer and recovery efficiency, and like most SRU issues, you typically wont know there’s a problem until its too late.
SRE can conduct an amine survey to minimize the hydrocarbon and BTEX contents in the amine acid gas. With that survey, CO2 slip and H2S pickup can also be maximized. This can also lead to optimizing the feed stream temperature to further maximize the initial conversion rates.
The SRU is only as good as what it receives, and how steady those feed streams are. This is why swings in flow and composition must be minimized, and when they do occur the equipment and operators have to ready to handle them.
Based on SRE’s testing experience, combustion air flow rates are always off by at least 10 – 20%, while this is normal it is important that these error rates are not heightened. When calibrating analyzers like the TGA, it is important that the proper calibration gases are used which represent a typical range for normal operations. And the cal gases must not be expired.
Our test have shown that the installation of a high efficiency mixing burner can add over 100 C to the potential RF temperature. For refineries, and when H2S qualities are low in gas plants, a front side split configuration is often best. It is important to optimize this setup with the proper flow fractions, and minimizing the amounts of air and nitrogen added to the system. This split flow setup requires that 1/3 of the total H2S be burned in order to have a 2:1 ratio of H2S to SO2 at the first converter.
Thanks for watching! For more videos on sulfur recovery, subscribe to our page. Also visit our website http://sulfurrecovery.com/, and sign up for our monthly newsletter here: http://sulfurrecovery.com/Newsletter/
Видео Optimizing the Reaction Furnace канала Sulfur Recovery Engineering Inc
The reaction furnace is the vessel where the thermal combustion reaction takes place. This is a Free-flame reaction inside a refractory lined vessel (corrosion related).
• This is also where the majority of the overall conversion of H2S to sulfur occurs (50 to 75%).
• There are many side reactions in the reaction furnace, creating unwanted products like CO, H2, COS and CS2
• For sufficient flame stability, a minimum temperature of 900 C (1650 F) is needed, however
• Temperatures above 1050 C are desired for the adequate destruction of contaminants like BTEX, mercaptans, NH3, HCN, methanol, HCs
• The reaction furnace is kinetically limited based on residence time, turbulence, and temperature, as well as burner efficiency.
The SRU is only as good as what it receives for feed streams. RF temperature is typically directly proportional to H2S content, this further illustrates the importance of the amine and SWS units. SRE can test these upstream units as well, optimizing for higher H2S contents and CO2 slip, and minimized hydrocarbon pickup.
In refineries, the sour water stripper sends a mixture of typically 1/3 H2S, 1/3, water, and 1/3 ammonia (NH3) to the SRU. If the ammonia is not fully destroyed in the reaction furnace, residuals can carry over to the condensers and converters, risking the formation of ammonia salts. These salts negatively impact heat transfer and recovery efficiency, and like most SRU issues, you typically wont know there’s a problem until its too late.
SRE can conduct an amine survey to minimize the hydrocarbon and BTEX contents in the amine acid gas. With that survey, CO2 slip and H2S pickup can also be maximized. This can also lead to optimizing the feed stream temperature to further maximize the initial conversion rates.
The SRU is only as good as what it receives, and how steady those feed streams are. This is why swings in flow and composition must be minimized, and when they do occur the equipment and operators have to ready to handle them.
Based on SRE’s testing experience, combustion air flow rates are always off by at least 10 – 20%, while this is normal it is important that these error rates are not heightened. When calibrating analyzers like the TGA, it is important that the proper calibration gases are used which represent a typical range for normal operations. And the cal gases must not be expired.
Our test have shown that the installation of a high efficiency mixing burner can add over 100 C to the potential RF temperature. For refineries, and when H2S qualities are low in gas plants, a front side split configuration is often best. It is important to optimize this setup with the proper flow fractions, and minimizing the amounts of air and nitrogen added to the system. This split flow setup requires that 1/3 of the total H2S be burned in order to have a 2:1 ratio of H2S to SO2 at the first converter.
Thanks for watching! For more videos on sulfur recovery, subscribe to our page. Also visit our website http://sulfurrecovery.com/, and sign up for our monthly newsletter here: http://sulfurrecovery.com/Newsletter/
Видео Optimizing the Reaction Furnace канала Sulfur Recovery Engineering Inc
Показать
Комментарии отсутствуют
Информация о видео
1 июня 2016 г. 21:42:30
00:03:38
Другие видео канала
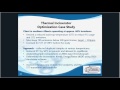
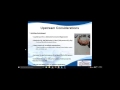
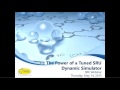
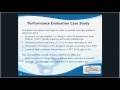

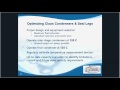
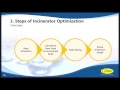
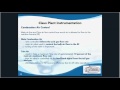
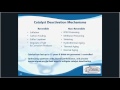
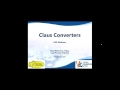
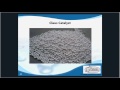

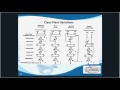
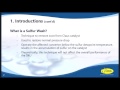

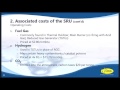
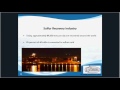