Engine Overhaul Part 3
Engine overhauls are extremely expensive. When it’s time to overhaul an engine, choosing a high-quality facility to do the job is important. The best way to choose where to send an engine is usually by personal referral. Ask other owners what shop(s) they have used and what the long-term results have been. Owners or operators that have put three to five hundred hours on an engine usually know by that time whether the overhaul was a good one. Low cylinder compressions, oil leaks or other problems are signs that the overhaul may not have been the best.
The first step in the overhaul process is determining that an engine does in fact need an overhaul. Mere time since the last overhaul doesn’t always equate to needing to overhaul an engine.
An overhaul always includes a complete disassembly of the engine, thorough cleaning and inspection of parts, repair of parts as needed and disposal of defective parts.
Major items such as the crankshaft, crankcase and connecting rods are subject to special inspections.
Parts are measured for excessive wear and proper clearances. The allowable dimensions and clearances are given in the manufacturer’s overhaul manual in two separate columns; one for manufacture (new) limits and one for service limits. The service limits are larger and allow for looser fits than manufacture limits. Some shops rebuild engines based on manufacture limits, while others use service limits.
The crankshaft is arguably the most important component in an aircraft engine. It absorbs the force generated by the reciprocating strokes of the pistons and rods and transforms it into rotational force for the propeller. The crankshaft is continuously subjected to loads and stresses from engine operation and the rotating propeller. Cracks or defects on a crankshaft can cause sudden engine failure or excessive, premature wear on the bearings. As a result, the crankshaft is probably the most inspected, measured and scrutinized part in the entire engine during the overhaul.
After engine disassembly, the crankshaft is cleaned and degreased in a chemical vat, dried and inspected. Most shops have a Magnaflux machine to inspect the crankshaft for cracks.
The crankcase provides the housing to hold all the internal components (crankshaft, camshaft, rods) as well as providing a place to attach the cylinders, accessory case and oil sump. The crankcase is made of cast aluminum and must be strong enough to absorb all the opposing forces of the engine as it is in operation.
Crankcases receive a thorough cleaning and inspection at overhaul.
Connecting rods are Magnafluxed, cleaned and dimensionally checked at overhaul. Connecting rod bearings along with the bolts and nuts that secure the rod halves are always replaced at overhaul. Connecting rod bushings are not always replaced, depending on the wear and condition on the bushings.
The rods are checked with special dowel tools to be sure they aren’t bent or twisted. The connecting rod is turned sideways and held in a vertical plane. One dowel slides through the connecting rod bushing and the other through the crankshaft bearing. After they are inserted, the ends of the dowels are laid on perfectly-matched metal blocks. The four ends of each dowel pin should lay perfectly flat if the rod is not twisted at all.
The camshaft and lifter bodies are generally replaced or sent out to be reground to remove any light scoring marks or surface deformities. The camshaft lobes go through a carburizing process to harden them at manufacture. The depth of the carburized layer of metal is not very deep (about fifteen-thousandths of an inch) and it is possible for machine shops to accidentally grind below that layer. The camshaft lobe would wear down rapidly once placed in use if that happened. Additionally, the lobes are not only elliptically shaped, but they have a slight taper across the top of the lobe to ensure that the lifter body spins as it contacts the lobe. It takes very precise machine work when grinding the lobe to maintain its original shape and the taper across the top. Camshafts should only be sent to high-quality, experienced machine shops like Aircraft Specialties for machining work.
The accessory case and oil sump are typically cleaned, inspected and reused. The Lycoming oil sumps that have intake pipes routed through the sump are reswedged around the intake pipe end to ensure there are no leaks down the road. This involves using a special tool which swells the pipe back out a little so that it forms a better seal when it is inserted into the sump opening.
Individual cylinder assemblies can be overhauled, but by the time the valves, guides and seats are replaced, the cost is almost equal to the cost of a new cylinder. Most overhaul facilities that I’m familiar with install new cylinders rather than overhauling the old ones.
Facebook
https://www.facebook.com/ESLAM.ELMASRY.2020
Twitter
https://twitter.com/Eng_Mech2009
Видео Engine Overhaul Part 3 канала Trucks Diagnosis إسلام المصري
The first step in the overhaul process is determining that an engine does in fact need an overhaul. Mere time since the last overhaul doesn’t always equate to needing to overhaul an engine.
An overhaul always includes a complete disassembly of the engine, thorough cleaning and inspection of parts, repair of parts as needed and disposal of defective parts.
Major items such as the crankshaft, crankcase and connecting rods are subject to special inspections.
Parts are measured for excessive wear and proper clearances. The allowable dimensions and clearances are given in the manufacturer’s overhaul manual in two separate columns; one for manufacture (new) limits and one for service limits. The service limits are larger and allow for looser fits than manufacture limits. Some shops rebuild engines based on manufacture limits, while others use service limits.
The crankshaft is arguably the most important component in an aircraft engine. It absorbs the force generated by the reciprocating strokes of the pistons and rods and transforms it into rotational force for the propeller. The crankshaft is continuously subjected to loads and stresses from engine operation and the rotating propeller. Cracks or defects on a crankshaft can cause sudden engine failure or excessive, premature wear on the bearings. As a result, the crankshaft is probably the most inspected, measured and scrutinized part in the entire engine during the overhaul.
After engine disassembly, the crankshaft is cleaned and degreased in a chemical vat, dried and inspected. Most shops have a Magnaflux machine to inspect the crankshaft for cracks.
The crankcase provides the housing to hold all the internal components (crankshaft, camshaft, rods) as well as providing a place to attach the cylinders, accessory case and oil sump. The crankcase is made of cast aluminum and must be strong enough to absorb all the opposing forces of the engine as it is in operation.
Crankcases receive a thorough cleaning and inspection at overhaul.
Connecting rods are Magnafluxed, cleaned and dimensionally checked at overhaul. Connecting rod bearings along with the bolts and nuts that secure the rod halves are always replaced at overhaul. Connecting rod bushings are not always replaced, depending on the wear and condition on the bushings.
The rods are checked with special dowel tools to be sure they aren’t bent or twisted. The connecting rod is turned sideways and held in a vertical plane. One dowel slides through the connecting rod bushing and the other through the crankshaft bearing. After they are inserted, the ends of the dowels are laid on perfectly-matched metal blocks. The four ends of each dowel pin should lay perfectly flat if the rod is not twisted at all.
The camshaft and lifter bodies are generally replaced or sent out to be reground to remove any light scoring marks or surface deformities. The camshaft lobes go through a carburizing process to harden them at manufacture. The depth of the carburized layer of metal is not very deep (about fifteen-thousandths of an inch) and it is possible for machine shops to accidentally grind below that layer. The camshaft lobe would wear down rapidly once placed in use if that happened. Additionally, the lobes are not only elliptically shaped, but they have a slight taper across the top of the lobe to ensure that the lifter body spins as it contacts the lobe. It takes very precise machine work when grinding the lobe to maintain its original shape and the taper across the top. Camshafts should only be sent to high-quality, experienced machine shops like Aircraft Specialties for machining work.
The accessory case and oil sump are typically cleaned, inspected and reused. The Lycoming oil sumps that have intake pipes routed through the sump are reswedged around the intake pipe end to ensure there are no leaks down the road. This involves using a special tool which swells the pipe back out a little so that it forms a better seal when it is inserted into the sump opening.
Individual cylinder assemblies can be overhauled, but by the time the valves, guides and seats are replaced, the cost is almost equal to the cost of a new cylinder. Most overhaul facilities that I’m familiar with install new cylinders rather than overhauling the old ones.
https://www.facebook.com/ESLAM.ELMASRY.2020
https://twitter.com/Eng_Mech2009
Видео Engine Overhaul Part 3 канала Trucks Diagnosis إسلام المصري
Показать
Комментарии отсутствуют
Информация о видео
30 августа 2021 г. 23:30:19
00:21:16
Другие видео канала
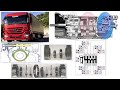
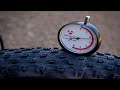
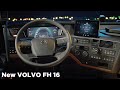
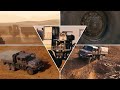
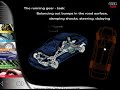

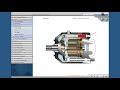
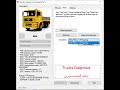

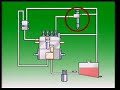
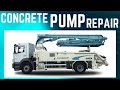
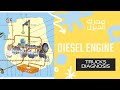
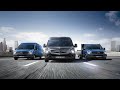
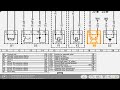
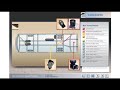
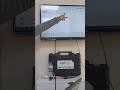
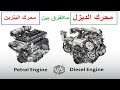
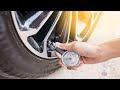
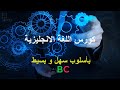
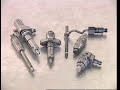