How to Design Wind Turbine Blade Geometry for Optimal Aerodynamic Efficiency
This is part 3 of my series: “How Does a Wind Turbine Work?” In this video I show you how to use the blade element momentum theory, BEM, that we discussed in the last videos, to design an efficient wind turbine rotor.
Topics include:
00:33 Lift equation
00:47 Optimum aerodynamic conditions with constant circulation along the span
01:05 How the local wind speed and angle vary along the length of the blade
01:22 How to change the chord and twist angle along the blade span
01:50 Why designers normally modify the chord distribution to have smaller chords at the root
02:28 The torque equation and why the tip's aerodynamics is more important than the root
02:52 What happens if you use a turbine at a different wind speed than it was designed for
03:46 How variable speed turbines can operate efficiently over a wind range of wind speeds
04:18 What is tip speed ratio (TSR) and why is it important to wind turbine designers?
04:48 Blade solidity
06:07 How to find a starting point in the wind turbine blade design process
07:22 Why are wind turbine blades getting so skinny?
07:54 Reducing wind turbine noise by limiting rotational speed
08:29The different requirements of aerofoils at the root versus tip of the blade
Check out part one and two of my “How Does a Wind Turbine Work?” series where I go through the mechanical engineering and aerodynamic theory needed to understand how a wind turbine works and design a wind turbine blade:
How Much Energy is in the Wind?
https://www.youtube.com/watch?v=7-awFXqisYA&t=7s
How to Calculate Wind Turbine Power Output: Blade Element Momentum Method
https://youtu.be/o6BCnhubbiQ
If you want to follow the derivations I mentioned in this video then check out section 3.7.2 of Burton's "Wind Energy Handbook."
Available to buy from Amazon (affiliate link), or your university library probably has it!
https://amzn.to/32Pb1fh
The optimum aerodynamic design equation at 6:10 has the following parameters:
sigma_r = chord solidity at the radial location (chord length divided by swept circumference at that radial location)
lambda = tip speed ratio (tip speed due to blade rotation (radial location times rotational speed) divided by wind speed)
C_l = local lift coefficient
mu = r/R (radial location divided by radius)
Видео How to Design Wind Turbine Blade Geometry for Optimal Aerodynamic Efficiency канала Engineering with Rosie
Topics include:
00:33 Lift equation
00:47 Optimum aerodynamic conditions with constant circulation along the span
01:05 How the local wind speed and angle vary along the length of the blade
01:22 How to change the chord and twist angle along the blade span
01:50 Why designers normally modify the chord distribution to have smaller chords at the root
02:28 The torque equation and why the tip's aerodynamics is more important than the root
02:52 What happens if you use a turbine at a different wind speed than it was designed for
03:46 How variable speed turbines can operate efficiently over a wind range of wind speeds
04:18 What is tip speed ratio (TSR) and why is it important to wind turbine designers?
04:48 Blade solidity
06:07 How to find a starting point in the wind turbine blade design process
07:22 Why are wind turbine blades getting so skinny?
07:54 Reducing wind turbine noise by limiting rotational speed
08:29The different requirements of aerofoils at the root versus tip of the blade
Check out part one and two of my “How Does a Wind Turbine Work?” series where I go through the mechanical engineering and aerodynamic theory needed to understand how a wind turbine works and design a wind turbine blade:
How Much Energy is in the Wind?
https://www.youtube.com/watch?v=7-awFXqisYA&t=7s
How to Calculate Wind Turbine Power Output: Blade Element Momentum Method
https://youtu.be/o6BCnhubbiQ
If you want to follow the derivations I mentioned in this video then check out section 3.7.2 of Burton's "Wind Energy Handbook."
Available to buy from Amazon (affiliate link), or your university library probably has it!
https://amzn.to/32Pb1fh
The optimum aerodynamic design equation at 6:10 has the following parameters:
sigma_r = chord solidity at the radial location (chord length divided by swept circumference at that radial location)
lambda = tip speed ratio (tip speed due to blade rotation (radial location times rotational speed) divided by wind speed)
C_l = local lift coefficient
mu = r/R (radial location divided by radius)
Видео How to Design Wind Turbine Blade Geometry for Optimal Aerodynamic Efficiency канала Engineering with Rosie
Показать
Комментарии отсутствуют
Информация о видео
Другие видео канала


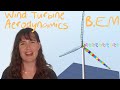


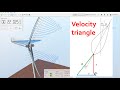
![[Concepts] How do Wind Turbine Rotors Really Work?](https://i.ytimg.com/vi/9EKPe873L80/default.jpg)
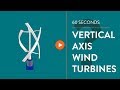
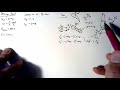
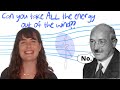
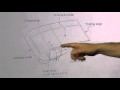
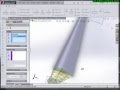
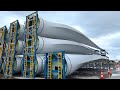
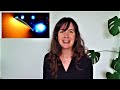
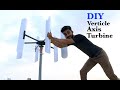

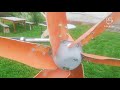
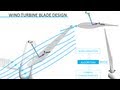

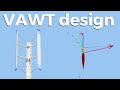