Threading away from the chuck non-inverting tool? Great Seal Bug Membrane Strainer pt 2
Cutting threads *away* from the chuck with the lathe in reverse and the tool on the back side of the part means you don't have to invert the tool. So much less stressful than threading towards the chuck. I cut almost all single point threads this way now, after watching Joe Pieczynski's video a few years back, although Joe inverted his cutter. Run it *behind* the workpiece and you don't need to invert it.
This thread is part of a membrane stretcher for my replica of The Great Seal Bug for BBC2 TV's "The Secret Genius of Modern Life" with Prof Hannah Fry.
Thin copper foil has crystal grains that allow it to be work-hardened by stretching. This mechanism strains metal membranes *almost* to breaking point . These metal diaphragms are for use in my reproduction of the Great Seal Bug for BBC2 TV with Prof Hannah Fry in The Secret Genius of Modern Life.
Copper has a Young's modulus of around 130 GPa, so a 140 mm circumference ring needs something like 0.5 Nm or 0.6 foot-pounds of torque on the nut to stretch 10 um foil the right amount. That's "not a lot", so we should be good to go IF I don't keep rupturing the foils.
Tension in the foil is more than 3 kN, which is ONE H*CK OF A LOT. See detailed notes at the end of this description.
AIMEE my Artificially Intelligent Machining and Engineering Expert system offers "helpful" advice as usual.
Links to tools and things. For the Amazon items, I get a tiny affiliate commission from each sale, it doesn't affect the price you pay and it helps me make more videos! First link to each item is Amazon.com, second (if there is one) is for UK/DE and some other countries if the same item is available on those sites.
Starrett 93B tap wrench https://amzn.to/3PQgpVX or https://amzn.to/3N21fLz
Edge Technology lathe chuck spider set https://amzn.to/3x0t5Rh
Notes about the mechanical advantage and my guesses at the torque
========================================================
Using a polished and rounded ring seems to work well, without any undue frictional effects. with a circumference around 140 mm and a thickness of 10 um, the CSA is 0.14 * 1e-5 or 1.4e-6 m^2. A Young's modulus of 130 GPa at 2% elastic strain in that cross-sectional area needs a stress of 1.3e11*1.4e-6*0.02 or 3.6 kN. Pushing the membrane to achieve a total of 5% strain with a 30mm diameter ring and a 44 mm diameter clamp means the sloping faces need to extend by 44*0.05/2 or 1.1 mm.
As the horizontal distance between clamp and ring is around 7mm, the hypotenuse will be 8.1 mm, the vertical distance moved by the ring will be around 4.2 mm and the angle of the slope will be around 31 degrees. It will actually be lower and steeper than that because of the curved face of the top clamp, so more like 3 mm and 40 degrees.
That's six turns of the screw at 0.5mm pitch. The force on the piston is roughly the tension times the sine of the slope, so about 2.3 kN. The mechanical advantage of the screw is about 112, less a lot for friction, so I need to apply a tangential force of maybe 50 N at 9mm radius, so 0.45 nM or 0.6 foot-pounds, which is less than that needed to tighten an N coaxial connector.
Chapters:
00:00 Here we go
06:16 Removing the ring
14:56 Body works
18:10 Knurling the Knob
23:39 External thread
27:43 Smoothing the Transition
Видео Threading away from the chuck non-inverting tool? Great Seal Bug Membrane Strainer pt 2 канала Machining and Microwaves
This thread is part of a membrane stretcher for my replica of The Great Seal Bug for BBC2 TV's "The Secret Genius of Modern Life" with Prof Hannah Fry.
Thin copper foil has crystal grains that allow it to be work-hardened by stretching. This mechanism strains metal membranes *almost* to breaking point . These metal diaphragms are for use in my reproduction of the Great Seal Bug for BBC2 TV with Prof Hannah Fry in The Secret Genius of Modern Life.
Copper has a Young's modulus of around 130 GPa, so a 140 mm circumference ring needs something like 0.5 Nm or 0.6 foot-pounds of torque on the nut to stretch 10 um foil the right amount. That's "not a lot", so we should be good to go IF I don't keep rupturing the foils.
Tension in the foil is more than 3 kN, which is ONE H*CK OF A LOT. See detailed notes at the end of this description.
AIMEE my Artificially Intelligent Machining and Engineering Expert system offers "helpful" advice as usual.
Links to tools and things. For the Amazon items, I get a tiny affiliate commission from each sale, it doesn't affect the price you pay and it helps me make more videos! First link to each item is Amazon.com, second (if there is one) is for UK/DE and some other countries if the same item is available on those sites.
Starrett 93B tap wrench https://amzn.to/3PQgpVX or https://amzn.to/3N21fLz
Edge Technology lathe chuck spider set https://amzn.to/3x0t5Rh
Notes about the mechanical advantage and my guesses at the torque
========================================================
Using a polished and rounded ring seems to work well, without any undue frictional effects. with a circumference around 140 mm and a thickness of 10 um, the CSA is 0.14 * 1e-5 or 1.4e-6 m^2. A Young's modulus of 130 GPa at 2% elastic strain in that cross-sectional area needs a stress of 1.3e11*1.4e-6*0.02 or 3.6 kN. Pushing the membrane to achieve a total of 5% strain with a 30mm diameter ring and a 44 mm diameter clamp means the sloping faces need to extend by 44*0.05/2 or 1.1 mm.
As the horizontal distance between clamp and ring is around 7mm, the hypotenuse will be 8.1 mm, the vertical distance moved by the ring will be around 4.2 mm and the angle of the slope will be around 31 degrees. It will actually be lower and steeper than that because of the curved face of the top clamp, so more like 3 mm and 40 degrees.
That's six turns of the screw at 0.5mm pitch. The force on the piston is roughly the tension times the sine of the slope, so about 2.3 kN. The mechanical advantage of the screw is about 112, less a lot for friction, so I need to apply a tangential force of maybe 50 N at 9mm radius, so 0.45 nM or 0.6 foot-pounds, which is less than that needed to tighten an N coaxial connector.
Chapters:
00:00 Here we go
06:16 Removing the ring
14:56 Body works
18:10 Knurling the Knob
23:39 External thread
27:43 Smoothing the Transition
Видео Threading away from the chuck non-inverting tool? Great Seal Bug Membrane Strainer pt 2 канала Machining and Microwaves
Показать
Комментарии отсутствуют
Информация о видео
Другие видео канала
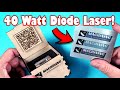
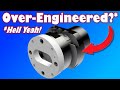

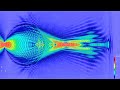
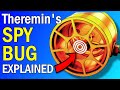
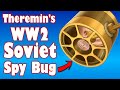

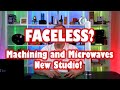
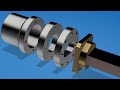
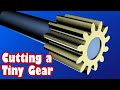


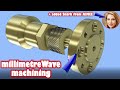
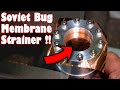



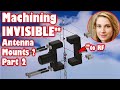
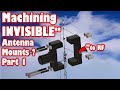
