A tour of DW Factory with John Good: exclusively for BeatIt
John Good shows http://en.beatit.tv/ drummers' website around the DW factory in Oxnard, CA.
http://en.beatit.tv/john-good-gives-beatit-a-tour-of-the-dw-factory/
During the factory tour, John Good showed us around the entire factory, which means you are about to see all the stages of the production process plus some of the people who make DW ideas a reality (the company has about 175 employees). You will see what John call ‘the cool part of this job’, which is the place where many kinds of wood sit before they go into production, e. g. European spalted beech or Tasmanian blackheart sassafras.
In the plywood shop, veneer is clipped to size before sheets are fitted together. You will see maple veneer (DW buy about 40,000 square meters of maple a month). Apart from maple, the company also uses cherry, birch, oak, gum, poplar and many more.
The video shows plies of purpleheart put together to become a drum shell. First, the sheets are glued together and put into a press in 200ºF (about 93,3ºC). Then, the press puts pressure of 3100 pounds per square inch. After 3 minutes a sheet of plywood is ready. The next step is to cut the plywood sheet to size.
A 12-inch shell consisting of 9 purpleheart plies is made in the clip. The plies are glued together in the following fashion: 3 sheets – vertical grain, long grain, vertical grain. Then, they are put into a hot press (2600 pounds per square inch) at 200ºF (about 93ºC) for 7.5 to 8 minutes, and a cold press to harden the shell and speed up the glue drying process. The technology is protected with a patent and applied to shells sized 6 to 24 inches, including the 23” kick drum.
You will also see the process of sanding shells, both on the inside and outside, as well as grinding the bearing edges (on toms, bass drums and snare drums) and cutting out the snare bed. John Good attaches significance to the snare bed. DW have engineered a machine that cuts it out consistently the same while retaining the profile of the bearing edge. Each snare bed is 6 ¼” long and is divided into three sections: taper (2 1/8” long), center (2” long, 3/32” deep), taper (2 1/8” long).
The only drum that DW put lacquer on the inside is the snare (all the others are oil-sealed) to make it sound bright. When the shell is put on a shelf, the lacquer has a tendency to run. John Good has come up with a special machine to sort that problem out, which you will also see in the video.
You will also be able to visit such departments as: custom graphics, clear lacquer, quality control, Black Nickel Over Brass, tuning, shell storage (e. g. Ivory ebony, Mapa burl, bird’s eye maple, African chenchen, etc.), pedal assembly and testing, stand production, R&D, John Good’s gallery, the Drum Channel studio, customer service, marketing, sales, shipping.
Basically, everything a DW fan, but also an all-around drum freak, would love to see…
Видео A tour of DW Factory with John Good: exclusively for BeatIt канала EN Beatit TV
http://en.beatit.tv/john-good-gives-beatit-a-tour-of-the-dw-factory/
During the factory tour, John Good showed us around the entire factory, which means you are about to see all the stages of the production process plus some of the people who make DW ideas a reality (the company has about 175 employees). You will see what John call ‘the cool part of this job’, which is the place where many kinds of wood sit before they go into production, e. g. European spalted beech or Tasmanian blackheart sassafras.
In the plywood shop, veneer is clipped to size before sheets are fitted together. You will see maple veneer (DW buy about 40,000 square meters of maple a month). Apart from maple, the company also uses cherry, birch, oak, gum, poplar and many more.
The video shows plies of purpleheart put together to become a drum shell. First, the sheets are glued together and put into a press in 200ºF (about 93,3ºC). Then, the press puts pressure of 3100 pounds per square inch. After 3 minutes a sheet of plywood is ready. The next step is to cut the plywood sheet to size.
A 12-inch shell consisting of 9 purpleheart plies is made in the clip. The plies are glued together in the following fashion: 3 sheets – vertical grain, long grain, vertical grain. Then, they are put into a hot press (2600 pounds per square inch) at 200ºF (about 93ºC) for 7.5 to 8 minutes, and a cold press to harden the shell and speed up the glue drying process. The technology is protected with a patent and applied to shells sized 6 to 24 inches, including the 23” kick drum.
You will also see the process of sanding shells, both on the inside and outside, as well as grinding the bearing edges (on toms, bass drums and snare drums) and cutting out the snare bed. John Good attaches significance to the snare bed. DW have engineered a machine that cuts it out consistently the same while retaining the profile of the bearing edge. Each snare bed is 6 ¼” long and is divided into three sections: taper (2 1/8” long), center (2” long, 3/32” deep), taper (2 1/8” long).
The only drum that DW put lacquer on the inside is the snare (all the others are oil-sealed) to make it sound bright. When the shell is put on a shelf, the lacquer has a tendency to run. John Good has come up with a special machine to sort that problem out, which you will also see in the video.
You will also be able to visit such departments as: custom graphics, clear lacquer, quality control, Black Nickel Over Brass, tuning, shell storage (e. g. Ivory ebony, Mapa burl, bird’s eye maple, African chenchen, etc.), pedal assembly and testing, stand production, R&D, John Good’s gallery, the Drum Channel studio, customer service, marketing, sales, shipping.
Basically, everything a DW fan, but also an all-around drum freak, would love to see…
Видео A tour of DW Factory with John Good: exclusively for BeatIt канала EN Beatit TV
Показать
Комментарии отсутствуют
Информация о видео
Другие видео канала

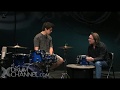
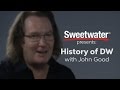
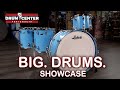
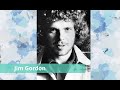
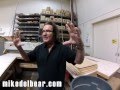
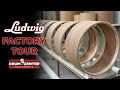
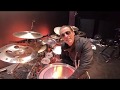

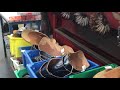
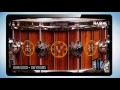
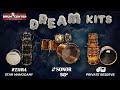


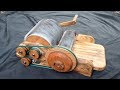
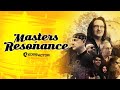

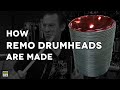

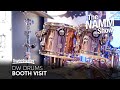