Problem Solving Basics - Root Cause Analysis
Our Problem-Solving Basics video is broken into eight different sections, each with its own point. Click "Show More" below to expand the description for links to each section, as well as a link that will direct you to additional training options offered by ThinkReliability.
What people believe about root cause analysis affects how they analyze, communicate and prevent problems. Cause-and-effect is not one of the tools to choose, but rather the basis of an objective, evidence-based, scientific approach. Regardless of the type or size of the problem, cause-and-effect applies. A problem analysis can begin with a simple 3- to 5-Why, then expand into as much detail as needed to thoroughly explain an issue.
This video:
- shows the confusion with common phrases like “contributing factor” and “root cause.”
- explains the three basic steps of problem-solving and shows how other methods align.
- shows how the problem-solving cycle reveals where work processes need to change.
- explains how addressing smaller problems can help prevent bigger problems from occurring.
Improving the way frontline personnel, technical leads and management communicate the specifics within a problem provides better access to insight, ideas and, ultimately, solutions.
The hyperlinked times below will help you navigate the eight sections of the video.
Start – Title page, contact information.
0:30– Concepts, method, skills
This section covers what people believe about conventional root cause analysis, definitions in our Cause Mapping® method, and an explanation of the fire triangle highlighting the contradiction with contributing cause and root cause.
2:07 – Definitions – analysis, system, cause
3:10 – Root cause analysis – conventional approach vs the Cause Mapping® method
The phrases contributing factor and root cause continue to create confusion when people attempt to explain how an issue occurred. The fire triangle is one of the easiest ways to illustrate how people have been miscommunicating these terms for over 50 years.
9:17 – The Cause Mapping® method - from 1-Why, through multiple 5-Whys to a 15-Why
analysis, mapping logic
This section of the video shows how an incident can be analyzed at different levels of detail and can incorporate different perspectives without causing disagreement (1-Why, 5-Why, 15-Why).
12:41 – Three problem-solving steps
All problem solving uses the same three steps: 1. Problem, 2. Analysis and 3. Solutions. With this, we find that 6-sigma, 8D, Kaizen, Fishbone among other methods are aligned. These basics are important to reinforce within a company to keep departments, people and approaches aligned. It’s the same basic steps for auto mechanics, engineers, doctors, operators and management.
13:45 – 6-sigma
14:10 – 8D (disciplines)
14:44 – Kaizen
14:56 – Fishbone (lean philosophy)
15:38 – Three basic steps for auto mechanics, engineers, doctors, operators and management
17:48 – How problem-solving changes from reactive to proactive
Continuous Improvement This section explores how problems and work processes connect (Plan-Do-Check-Act) and how different tools align around analyzing a problem and performing a work process (the approach of High Reliability Organizations).
23:28 – Consistent approach
This section shows how, regardless of type or size, problem analyses begin with 3- to 5-Whys, then expand as needed. Plus, I cover how accurate communication between frontline, technical leads and management is an essential part of an organization’s problem-solving culture.
28:23 – Close – Contact information and links to other videos
Want to learn more about the Cause Mapping method of root cause analysis? Consider joining one of our upcoming free webinars or other online training options: https://bit.ly/3afGjxf.
Chapters:
0:00 Title page, contact information
0:30 Concepts, method, skills
2:07 Definitions – analysis, system, cause
3:10 Root cause analysis
9:17 The Cause Mapping® method
12:41 Three problem-solving steps
13:45 6-sigma,
14:10 8D (disciplines)
14:44 Kaizen
14:56 Fishbone (lean philosophy)
15:38 Three basic steps
17:48 How problem-solving changes
23:28 Consistent approach
28:23 Contact information and links to other videos
Видео Problem Solving Basics - Root Cause Analysis канала CauseMapping
What people believe about root cause analysis affects how they analyze, communicate and prevent problems. Cause-and-effect is not one of the tools to choose, but rather the basis of an objective, evidence-based, scientific approach. Regardless of the type or size of the problem, cause-and-effect applies. A problem analysis can begin with a simple 3- to 5-Why, then expand into as much detail as needed to thoroughly explain an issue.
This video:
- shows the confusion with common phrases like “contributing factor” and “root cause.”
- explains the three basic steps of problem-solving and shows how other methods align.
- shows how the problem-solving cycle reveals where work processes need to change.
- explains how addressing smaller problems can help prevent bigger problems from occurring.
Improving the way frontline personnel, technical leads and management communicate the specifics within a problem provides better access to insight, ideas and, ultimately, solutions.
The hyperlinked times below will help you navigate the eight sections of the video.
Start – Title page, contact information.
0:30– Concepts, method, skills
This section covers what people believe about conventional root cause analysis, definitions in our Cause Mapping® method, and an explanation of the fire triangle highlighting the contradiction with contributing cause and root cause.
2:07 – Definitions – analysis, system, cause
3:10 – Root cause analysis – conventional approach vs the Cause Mapping® method
The phrases contributing factor and root cause continue to create confusion when people attempt to explain how an issue occurred. The fire triangle is one of the easiest ways to illustrate how people have been miscommunicating these terms for over 50 years.
9:17 – The Cause Mapping® method - from 1-Why, through multiple 5-Whys to a 15-Why
analysis, mapping logic
This section of the video shows how an incident can be analyzed at different levels of detail and can incorporate different perspectives without causing disagreement (1-Why, 5-Why, 15-Why).
12:41 – Three problem-solving steps
All problem solving uses the same three steps: 1. Problem, 2. Analysis and 3. Solutions. With this, we find that 6-sigma, 8D, Kaizen, Fishbone among other methods are aligned. These basics are important to reinforce within a company to keep departments, people and approaches aligned. It’s the same basic steps for auto mechanics, engineers, doctors, operators and management.
13:45 – 6-sigma
14:10 – 8D (disciplines)
14:44 – Kaizen
14:56 – Fishbone (lean philosophy)
15:38 – Three basic steps for auto mechanics, engineers, doctors, operators and management
17:48 – How problem-solving changes from reactive to proactive
Continuous Improvement This section explores how problems and work processes connect (Plan-Do-Check-Act) and how different tools align around analyzing a problem and performing a work process (the approach of High Reliability Organizations).
23:28 – Consistent approach
This section shows how, regardless of type or size, problem analyses begin with 3- to 5-Whys, then expand as needed. Plus, I cover how accurate communication between frontline, technical leads and management is an essential part of an organization’s problem-solving culture.
28:23 – Close – Contact information and links to other videos
Want to learn more about the Cause Mapping method of root cause analysis? Consider joining one of our upcoming free webinars or other online training options: https://bit.ly/3afGjxf.
Chapters:
0:00 Title page, contact information
0:30 Concepts, method, skills
2:07 Definitions – analysis, system, cause
3:10 Root cause analysis
9:17 The Cause Mapping® method
12:41 Three problem-solving steps
13:45 6-sigma,
14:10 8D (disciplines)
14:44 Kaizen
14:56 Fishbone (lean philosophy)
15:38 Three basic steps
17:48 How problem-solving changes
23:28 Consistent approach
28:23 Contact information and links to other videos
Видео Problem Solving Basics - Root Cause Analysis канала CauseMapping
Показать
Комментарии отсутствуют
Информация о видео
Другие видео канала


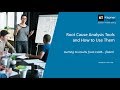


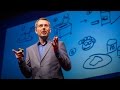


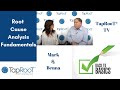
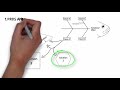

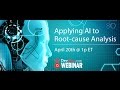

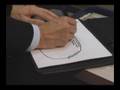
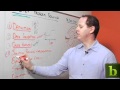

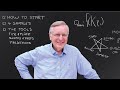
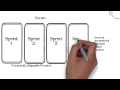
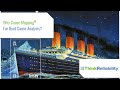
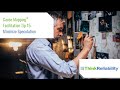