Build Your Own Hot Wire Foam Cutter - Professional Tools for Modelers
A hot wire foam cutter is a must for anyone who is serious about modeling with foam. Foam is an extremely useful and versatile material when it comes to model making but to truly get the most out of it you need the right tools.
Building your own hot wire foam cutter is very easy and once you know how they work you can build all types of different foam cutters for an infinite range of jobs.
The foam cutter I’m making today is a tabletop precision foam cutter used for making very precise straight cuts.
Additionally by incorporating the temperature controller into the wiring I now have complete control over how hot the wire is. Controlling the wire temperature is vital for getting the perfect cut, too hot and the foam will melt before it even touches the wire… too cold and the wire will start to flex giving imprecise angles!
*Materials*
WOOD:
12mm MDF – Main cutting surface 30cm Wide 60cm Long
3mm MDF – Fascia 62cm Tall 30cm wide
30mm by 42mm Pine – Side support 2 strips 60cm long
30mm by 6mm Pine – Additional strip on side support 2 strips 60cm long and Controller block support
19mm by 42mm Pine – Cross section support 24cm long
MAIN ARM AND BASE
19mm Washer – Protects cutting surface from the hot wire
6mm Steel Rod – Main supporting arm at least 75cm long
6mm Saddle Clips – 6 in total
18 Gauge Galvanized Steel Wire – Hook in the top of the supporting arm
ELECTRONIS AND WIRES
12v DPDT Push On/Push Off Switch with inbuilt LED
2.1mm Bulkhead DC Power Connector
12v 8amp PWM Controller
10amp Screw Terminal Strip
Various Heat Shrink Tubes
Lead Solder
10amp 3mm Electrical Cable Red & Black
3mm Washer – times 2, Soldered to the ends of the output wires from the temperature controller
NICHROME WIRE
28 Gauge Nichrome Wire
3mm Washer – Attached to nichrome wire
5mm Diameter Spring, 1cm Long – Optional to absorb excess slack as nichrome wire heats up
CLAMP
3mm Diameter, 35mm Long Round Head Bolt
3mm Nut – times 2
3mm Washer – times 2
3mm Wing Nut
Tips for using the Hot Wire Foam Cutter:
A good starting temperature to aim for when cutting foam is 600°F, that temperature will vary depending on the density of the foam of course.
Try to use a lower temperature rather than a high temperature, the foam is more forgiving when cutting at lower temperatures and you’ll generally end up with a nicer finish.
Don’t forget as you can see in the video, you can make templates using regular printer paper and use that as a stencil for making cuts. This is where you need to ensure the wire temperature is not too high otherwise the wire will cut straight through the paper as well.
Avoid stopping during a cut, if you stop and start whilst cutting you may end up with fault lines where you stopped. Again a lower temperature will help minimize lines due to stopping and starting but for best result try to complete the cut in one smooth motion.
You can clamp sections of wood to your cutting surface to use as a guide for getting perfectly straight cuts, you can also temporarily glue thin strips of wood to the surface of the foam to get the same effect, essentially you’ll use the strips of wood that are glued directly to the foam as a guide allowing you to achieve all sorts of complex cuts.
MUSIC
Intro Music
Premium Beat – Green Screen
Background Music
Rhodesia by Twin Musicom is licensed under a Creative Commons Attribution license (https://creativecommons.org/licenses/by/4.0/)
Artist: http://www.twinmusicom.org/
Видео Build Your Own Hot Wire Foam Cutter - Professional Tools for Modelers канала Luke Towan
Building your own hot wire foam cutter is very easy and once you know how they work you can build all types of different foam cutters for an infinite range of jobs.
The foam cutter I’m making today is a tabletop precision foam cutter used for making very precise straight cuts.
Additionally by incorporating the temperature controller into the wiring I now have complete control over how hot the wire is. Controlling the wire temperature is vital for getting the perfect cut, too hot and the foam will melt before it even touches the wire… too cold and the wire will start to flex giving imprecise angles!
*Materials*
WOOD:
12mm MDF – Main cutting surface 30cm Wide 60cm Long
3mm MDF – Fascia 62cm Tall 30cm wide
30mm by 42mm Pine – Side support 2 strips 60cm long
30mm by 6mm Pine – Additional strip on side support 2 strips 60cm long and Controller block support
19mm by 42mm Pine – Cross section support 24cm long
MAIN ARM AND BASE
19mm Washer – Protects cutting surface from the hot wire
6mm Steel Rod – Main supporting arm at least 75cm long
6mm Saddle Clips – 6 in total
18 Gauge Galvanized Steel Wire – Hook in the top of the supporting arm
ELECTRONIS AND WIRES
12v DPDT Push On/Push Off Switch with inbuilt LED
2.1mm Bulkhead DC Power Connector
12v 8amp PWM Controller
10amp Screw Terminal Strip
Various Heat Shrink Tubes
Lead Solder
10amp 3mm Electrical Cable Red & Black
3mm Washer – times 2, Soldered to the ends of the output wires from the temperature controller
NICHROME WIRE
28 Gauge Nichrome Wire
3mm Washer – Attached to nichrome wire
5mm Diameter Spring, 1cm Long – Optional to absorb excess slack as nichrome wire heats up
CLAMP
3mm Diameter, 35mm Long Round Head Bolt
3mm Nut – times 2
3mm Washer – times 2
3mm Wing Nut
Tips for using the Hot Wire Foam Cutter:
A good starting temperature to aim for when cutting foam is 600°F, that temperature will vary depending on the density of the foam of course.
Try to use a lower temperature rather than a high temperature, the foam is more forgiving when cutting at lower temperatures and you’ll generally end up with a nicer finish.
Don’t forget as you can see in the video, you can make templates using regular printer paper and use that as a stencil for making cuts. This is where you need to ensure the wire temperature is not too high otherwise the wire will cut straight through the paper as well.
Avoid stopping during a cut, if you stop and start whilst cutting you may end up with fault lines where you stopped. Again a lower temperature will help minimize lines due to stopping and starting but for best result try to complete the cut in one smooth motion.
You can clamp sections of wood to your cutting surface to use as a guide for getting perfectly straight cuts, you can also temporarily glue thin strips of wood to the surface of the foam to get the same effect, essentially you’ll use the strips of wood that are glued directly to the foam as a guide allowing you to achieve all sorts of complex cuts.
MUSIC
Intro Music
Premium Beat – Green Screen
Background Music
Rhodesia by Twin Musicom is licensed under a Creative Commons Attribution license (https://creativecommons.org/licenses/by/4.0/)
Artist: http://www.twinmusicom.org/
Видео Build Your Own Hot Wire Foam Cutter - Professional Tools for Modelers канала Luke Towan
Показать
Комментарии отсутствуют
Информация о видео
Другие видео канала



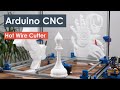


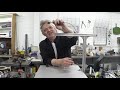





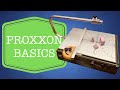
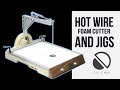

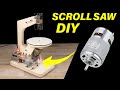

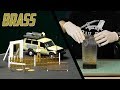

