CNC Oxyfuel Cutting Machine by TL PATHAK GROUP KOLKATA#cnc #steelcutting #heavyengineering #machine
The CNC Oxyfuel Cutting Machine offered by TL Pathak Group, based in Kolkata, is a robust and high-performance industrial solution designed for the automated thermal cutting of ferrous metals, primarily mild steel and low-alloy steels, especially in thicker plates. Combining the precision of Computer Numerical Control (CNC) with the power of the oxyfuel cutting process, this machine delivers accuracy, repeatability, and efficiency for demanding metal fabrication tasks.
Core Technology:
CNC (Computer Numerical Control): The machine's movements (along X, Y, and potentially Z axes) are precisely guided by a dedicated CNC controller. Users can input cutting paths directly or load them from standard CAD/CAM software (typically via G-code). This ensures intricate shapes, complex contours, and simple straight lines are cut with high accuracy and minimal operator intervention.
Oxyfuel Cutting Process: This thermal cutting method utilizes a mixture of a fuel gas (like Acetylene, LPG, or Propane) and pure oxygen.
Preheating: A flame generated by the fuel gas and oxygen heats the steel surface to its ignition temperature (around 870°C / 1600°F).
Cutting: A high-pressure jet of pure oxygen is then directed onto the preheated spot. This oxygen rapidly oxidizes (burns) the iron, creating molten slag (iron oxide). The kinetic energy of the oxygen jet blows this molten slag away, creating the kerf or cut. This process is highly effective for cutting thicker carbon steel sections.
Key Features & Components (Typical configuration, specific models may vary):
Robust Gantry Structure: A heavy-duty bridge or gantry system spans the cutting area, carrying the cutting torch(es). This ensures stability and vibration-free movement for precise cuts, even over large working areas.
Precision Drive System: Utilizes high-quality servo motors or stepper motors with precision gearboxes and rack-and-pinion or ball screw drives for smooth, accurate, and fast positioning of the cutting head.
Multiple Cutting Torches (Optional): Can be configured with single or multiple oxyfuel torches for simultaneous cutting (e.g., strip cutting) to increase productivity.
Automatic Torch Height Control (THC): Often included to maintain a consistent distance between the torch tip and the workpiece, compensating for uneven plate surfaces and ensuring optimal cut quality and consumable life.
Advanced CNC Controller: User-friendly interface, often with a graphical display, large memory for program storage, standard shape library, nesting capabilities (optional software), and diagnostic features. Supports standard G-code formats.
Gas Control System: Automated solenoids and regulators for precise control of preheat gases (fuel gas + oxygen) and the cutting oxygen flow, often managed directly by the CNC program for different material thicknesses. Includes safety features like flashback arrestors.
Heavy-Duty Cutting Table: A sturdy table (often with replaceable slats or a water bed option) designed to support heavy steel plates and withstand the rigours of the cutting process. Water tables help reduce fume emission and plate distortion.
Fume Extraction System (Optional): Can be integrated with downdraft tables or fume extraction hoods to remove smoke and fumes generated during cutting, improving the working environment and safety.
Automatic Ignition System: For safe and convenient lighting of the preheat flames.
Advantages & Benefits:
Cost-Effective for Thick Steel: Oxyfuel cutting is generally the most economical process for cutting carbon steel plates thicker than approximately 1-2 inches (25-50 mm), compared to plasma or laser.
High Cutting Thickness Capability: Can cut very thick steel sections (several inches or even over a foot, depending on the specific setup).
Good Cut Edge Quality: Produces relatively smooth, square cut edges on thicker materials when parameters are set correctly.
Automation & Precision: CNC control ensures high accuracy (+/- tolerance depends on model/setup) and repeatability, reducing manual labor and errors.
Efficiency: Automated cutting and optional multiple torches significantly increase productivity compared to manual cutting methods.
Versatility: Capable of cutting complex shapes and profiles directly from digital designs.
Local Support (Kolkata): Sourcing from TL Pathak Group in Kolkata potentially offers advantages in terms of installation, service, spare parts availability, and understanding local operational conditions.
Typical Applications & Industries:
Heavy Engineering & Fabrication
Shipbuilding and Repair
Bridge Construction
Manufacturing of Construction Machinery & Earthmoving Equipment
Pressure Vessel Manufacturing
Steel Service Centers
Railway Wagon Manufacturing
General Steel Fabrication Shops
#CNCOxyfuel #OxyfuelCutting #CNCCutting #ThermalCutting #SteelCutting #PlateCutting #MetalFabrication #HeavyEngineering #Shipbuilding #TLPathakGroup #PathakMachines #MakeInIndia #KolkataManufacturing #Ind
Видео CNC Oxyfuel Cutting Machine by TL PATHAK GROUP KOLKATA#cnc #steelcutting #heavyengineering #machine канала TL Pathak Group - Machines For Future
Core Technology:
CNC (Computer Numerical Control): The machine's movements (along X, Y, and potentially Z axes) are precisely guided by a dedicated CNC controller. Users can input cutting paths directly or load them from standard CAD/CAM software (typically via G-code). This ensures intricate shapes, complex contours, and simple straight lines are cut with high accuracy and minimal operator intervention.
Oxyfuel Cutting Process: This thermal cutting method utilizes a mixture of a fuel gas (like Acetylene, LPG, or Propane) and pure oxygen.
Preheating: A flame generated by the fuel gas and oxygen heats the steel surface to its ignition temperature (around 870°C / 1600°F).
Cutting: A high-pressure jet of pure oxygen is then directed onto the preheated spot. This oxygen rapidly oxidizes (burns) the iron, creating molten slag (iron oxide). The kinetic energy of the oxygen jet blows this molten slag away, creating the kerf or cut. This process is highly effective for cutting thicker carbon steel sections.
Key Features & Components (Typical configuration, specific models may vary):
Robust Gantry Structure: A heavy-duty bridge or gantry system spans the cutting area, carrying the cutting torch(es). This ensures stability and vibration-free movement for precise cuts, even over large working areas.
Precision Drive System: Utilizes high-quality servo motors or stepper motors with precision gearboxes and rack-and-pinion or ball screw drives for smooth, accurate, and fast positioning of the cutting head.
Multiple Cutting Torches (Optional): Can be configured with single or multiple oxyfuel torches for simultaneous cutting (e.g., strip cutting) to increase productivity.
Automatic Torch Height Control (THC): Often included to maintain a consistent distance between the torch tip and the workpiece, compensating for uneven plate surfaces and ensuring optimal cut quality and consumable life.
Advanced CNC Controller: User-friendly interface, often with a graphical display, large memory for program storage, standard shape library, nesting capabilities (optional software), and diagnostic features. Supports standard G-code formats.
Gas Control System: Automated solenoids and regulators for precise control of preheat gases (fuel gas + oxygen) and the cutting oxygen flow, often managed directly by the CNC program for different material thicknesses. Includes safety features like flashback arrestors.
Heavy-Duty Cutting Table: A sturdy table (often with replaceable slats or a water bed option) designed to support heavy steel plates and withstand the rigours of the cutting process. Water tables help reduce fume emission and plate distortion.
Fume Extraction System (Optional): Can be integrated with downdraft tables or fume extraction hoods to remove smoke and fumes generated during cutting, improving the working environment and safety.
Automatic Ignition System: For safe and convenient lighting of the preheat flames.
Advantages & Benefits:
Cost-Effective for Thick Steel: Oxyfuel cutting is generally the most economical process for cutting carbon steel plates thicker than approximately 1-2 inches (25-50 mm), compared to plasma or laser.
High Cutting Thickness Capability: Can cut very thick steel sections (several inches or even over a foot, depending on the specific setup).
Good Cut Edge Quality: Produces relatively smooth, square cut edges on thicker materials when parameters are set correctly.
Automation & Precision: CNC control ensures high accuracy (+/- tolerance depends on model/setup) and repeatability, reducing manual labor and errors.
Efficiency: Automated cutting and optional multiple torches significantly increase productivity compared to manual cutting methods.
Versatility: Capable of cutting complex shapes and profiles directly from digital designs.
Local Support (Kolkata): Sourcing from TL Pathak Group in Kolkata potentially offers advantages in terms of installation, service, spare parts availability, and understanding local operational conditions.
Typical Applications & Industries:
Heavy Engineering & Fabrication
Shipbuilding and Repair
Bridge Construction
Manufacturing of Construction Machinery & Earthmoving Equipment
Pressure Vessel Manufacturing
Steel Service Centers
Railway Wagon Manufacturing
General Steel Fabrication Shops
#CNCOxyfuel #OxyfuelCutting #CNCCutting #ThermalCutting #SteelCutting #PlateCutting #MetalFabrication #HeavyEngineering #Shipbuilding #TLPathakGroup #PathakMachines #MakeInIndia #KolkataManufacturing #Ind
Видео CNC Oxyfuel Cutting Machine by TL PATHAK GROUP KOLKATA#cnc #steelcutting #heavyengineering #machine канала TL Pathak Group - Machines For Future
CNC Oxyfuel Cutting Machine Oxy-Acetylene Cutting Oxy-Propane Cutting CNC Gas Cutting Automated Steel Cutting Thick Steel Plate Cutting TL Pathak Group Industrial Machinery Metal Cutting Equipment Gantry Cutting Machine CNC Profile Cutting Steel Fabrication Machinery Heavy Duty Cutting Manufacturing Technology Metalworking CNC Automation Ferrous Metal Cutting PATHAK INDUSTRIES KOL PATHAK MACHINES INDUSTRIES PATHAK MACHINE TOOLS PATHAK INDUSTRIES LLP INDIA
Комментарии отсутствуют
Информация о видео
25 апреля 2025 г. 14:52:41
00:00:28
Другие видео канала

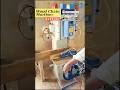

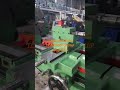
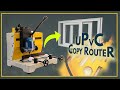


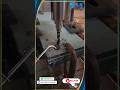

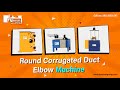