Knifemaking: Kitchen Knife Made With Scrap High Carbon Steel
Making a fine cutting tool out of cheap materials and scrap pieces, using many of my homemade tools and jigs and various vintage equipment I restored in videos during my years on YouTube!
I forgot to measure the end product on camera so here are the specs:
The blade ended up 145mm long and 45mm at the widest. Overall lentght 255mm, thickness tapered from 3.5mm to zero. Steel is 1070 (aka C70) high carbon steel, differentially heat treated with edge hardness between 50 and 55 Rockwell.
Handle is made of tabilized okumè and olive burl wood, with red (and a line of grey) felt liners, fixed to the tang just by friction in a japanese traditional way with split dowel.
Here are some of the videos where I go in more details about some of the tecniques used in this video:
Stabilizing wood: https://youtu.be/E-P3KWctkk0
Homemade Liners: https://youtu.be/8tIaEAXYv-k
Dedicated hamon video: https://youtu.be/hk8S1FQWXek
And here are some of the videos about the tools I used:
Fullering jig: https://youtu.be/zVbi4OYXxgY
File Guide: https://youtu.be/YNpr7SB-CMw
Hardening oven: https://youtu.be/5MNwqwmrWgQ
Tempering oven: https://youtu.be/uILynSeLuzU
Vacuum pump and chamber used to stabilize: https://youtu.be/BeiW_37rS-U
My lovely drill press: https://youtu.be/BZmqVw7MJsg
Grinder - Buffer: https://youtu.be/8V9f0DIkb90
I just started to list some of the stuff I use for my projects in this amazon storefront:
https://www.amazon.com/shop/blackbeardprojects
It's affiliate marketing, so if you order something from here you'll help the channel for free! Thank you!
Index of operation and materials:
0:22 Isolate tang material with my new fullering jig
0:41 Forge down the tang
1:16 Forge Blade Rough shape
1:32 Forge Bevels
2:00 Annhealed off camera by slowly cooling it with the forge
2:16 Grind profile with 2x72 belt grinder
2:50 Clean tang transition with homemade file guide
3:14 Grind radious with die grinder and round stone bit
3:34 Bevels fough grind
4:00 Apply exhaust pipe sealer to differentialy harden the blade
4:52 Hardening: Heat to 825°c and quench in 80°c oil
5:25 Removing scales with steel wire wheel on bench grinder
5:40 Tempering: Heat to 200°c for 2hrs
5:57 Final Grind of bevels, keeping blade cool with water
6:30 Hand sanding bevels up to 1200grit (also buffed off camera to a mirror polish)
7:02 Etch with ferric chloride to reveal hamon line
7:10 Clean and neutralize acid and remove oxide layer with fine steel whool
7:40 Prepare wood for handle cut to lenght with hand saw and to size with metal cutting band saw
8:00 Stabilize wood, process explained in detail in another video
9:40 Make red felt and gray cardstock liner, process explained in detail in another video
11:07 Glue handle stack with epoxy resin
11:30 Grind handle stock quare
11:44 Drill 10mm hole with drill press
12:14 Grind handle into octagon (some footage was lost here, sorry)
12:34 Split dowel with metal cutting bandsaw
12:45 Assemble knife with a bit of white mineral oil
13:05 Press friction fit
13:10 Strop on leather with fine polishing coumpount to get the sharp edge, bevels ground to zero, no secondary bevel.
Thanks a lot for watching, I hope you liked the video!
Suggestions and comments are welcome.
Leave a like and share to anyone who might be interested!
★Patreon★
https://www.patreon.com/blackbeardprojects
★Website★
http://blackbeardproject.com/
★Follow me★
Facebook ► https://www.facebook.com/BlackBeardProjects/
Twitter ► https://twitter.com/BlackBeardProje
Instagram ► https://www.instagram.com/black_beard_projects/
Видео Knifemaking: Kitchen Knife Made With Scrap High Carbon Steel канала Black Beard Projects
I forgot to measure the end product on camera so here are the specs:
The blade ended up 145mm long and 45mm at the widest. Overall lentght 255mm, thickness tapered from 3.5mm to zero. Steel is 1070 (aka C70) high carbon steel, differentially heat treated with edge hardness between 50 and 55 Rockwell.
Handle is made of tabilized okumè and olive burl wood, with red (and a line of grey) felt liners, fixed to the tang just by friction in a japanese traditional way with split dowel.
Here are some of the videos where I go in more details about some of the tecniques used in this video:
Stabilizing wood: https://youtu.be/E-P3KWctkk0
Homemade Liners: https://youtu.be/8tIaEAXYv-k
Dedicated hamon video: https://youtu.be/hk8S1FQWXek
And here are some of the videos about the tools I used:
Fullering jig: https://youtu.be/zVbi4OYXxgY
File Guide: https://youtu.be/YNpr7SB-CMw
Hardening oven: https://youtu.be/5MNwqwmrWgQ
Tempering oven: https://youtu.be/uILynSeLuzU
Vacuum pump and chamber used to stabilize: https://youtu.be/BeiW_37rS-U
My lovely drill press: https://youtu.be/BZmqVw7MJsg
Grinder - Buffer: https://youtu.be/8V9f0DIkb90
I just started to list some of the stuff I use for my projects in this amazon storefront:
https://www.amazon.com/shop/blackbeardprojects
It's affiliate marketing, so if you order something from here you'll help the channel for free! Thank you!
Index of operation and materials:
0:22 Isolate tang material with my new fullering jig
0:41 Forge down the tang
1:16 Forge Blade Rough shape
1:32 Forge Bevels
2:00 Annhealed off camera by slowly cooling it with the forge
2:16 Grind profile with 2x72 belt grinder
2:50 Clean tang transition with homemade file guide
3:14 Grind radious with die grinder and round stone bit
3:34 Bevels fough grind
4:00 Apply exhaust pipe sealer to differentialy harden the blade
4:52 Hardening: Heat to 825°c and quench in 80°c oil
5:25 Removing scales with steel wire wheel on bench grinder
5:40 Tempering: Heat to 200°c for 2hrs
5:57 Final Grind of bevels, keeping blade cool with water
6:30 Hand sanding bevels up to 1200grit (also buffed off camera to a mirror polish)
7:02 Etch with ferric chloride to reveal hamon line
7:10 Clean and neutralize acid and remove oxide layer with fine steel whool
7:40 Prepare wood for handle cut to lenght with hand saw and to size with metal cutting band saw
8:00 Stabilize wood, process explained in detail in another video
9:40 Make red felt and gray cardstock liner, process explained in detail in another video
11:07 Glue handle stack with epoxy resin
11:30 Grind handle stock quare
11:44 Drill 10mm hole with drill press
12:14 Grind handle into octagon (some footage was lost here, sorry)
12:34 Split dowel with metal cutting bandsaw
12:45 Assemble knife with a bit of white mineral oil
13:05 Press friction fit
13:10 Strop on leather with fine polishing coumpount to get the sharp edge, bevels ground to zero, no secondary bevel.
Thanks a lot for watching, I hope you liked the video!
Suggestions and comments are welcome.
Leave a like and share to anyone who might be interested!
★Patreon★
https://www.patreon.com/blackbeardprojects
★Website★
http://blackbeardproject.com/
★Follow me★
Facebook ► https://www.facebook.com/BlackBeardProjects/
Twitter ► https://twitter.com/BlackBeardProje
Instagram ► https://www.instagram.com/black_beard_projects/
Видео Knifemaking: Kitchen Knife Made With Scrap High Carbon Steel канала Black Beard Projects
Показать
Комментарии отсутствуют
Информация о видео
Другие видео канала
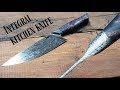
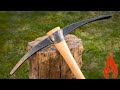

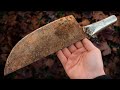
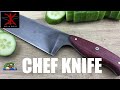
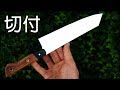
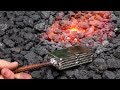
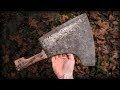
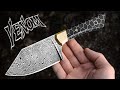
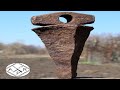

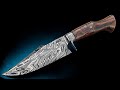

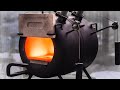
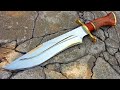
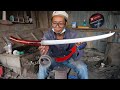

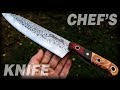

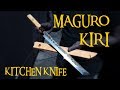